Braided Metal Hose
Javascript DHTML Drop Down Menu Powered by dhtml-menu-builder.com
|
When to use Corrugated Metal Hose
There are many different types of hose available on the market, including metal, rubber,
composite, PTFE, and fabric. The decision of which hose type to buy depends on the
application for which the hose is being used. Generally, there are eight factors that should
alert you to consider using metal hose:
1. TEMPERATURE EXTREMES
If either the temperature of the media going through the hose or the surrounding
atmospheric temperature is very cold or hot, metal may be the only material that
can withstand such temperature extremes.
2. CHEMICAL COMPATIBILITY
Metal hose can handle a wider variety of chemicals than most other hose
types. If the hose witt be exposed to aggressive chemicals (either internally or
externally), metal hose should be considered.
3. PERMEATION CONCERNS
Non·metal hose is susceptible to gas permeation through the hose wall
and into the atmosphere. Metal hose, on the other hand, does not allow
permeation. If contaning the gases inside the hose is important, metal hose may
be required.
4. POTENTIAL FOR CATASTROPHIC FAILURE
When a metal hose fails, it usually develops small holes or cracks. Other hose
types tend to develop larger cracks or come apart completely. If a sudden hose
failure is potentially catastrophic, a metal hose may help minimize the effects of
a failure by leaking product at a slower rate.
5. ABRASION AND OVERBENDING CONCERNS
To prevent abrasion and overbending, a metal hose can be used as a protective
cover over wires or even other hoses.
6. FIRE SAFETY
Other hose types will melt when exposed to fire, while metal hose maintains its
integrity up to 1300 degree F. (See NAHAD derating chart on page 33)
7. ACHIEVING FULL VACUUM
Under full vacuum, metal hose maintains its shape while other hose types
may collapse.
8. FLEXIBILITY IN FITTING CONFIGURATION
Virtually any type of fitting can be attached to metal hose, while other hose types
require special shanks and collars. |
Assembly Components
In this section, we will discuss the various components that make up a corrugated metal hose assembly,
and what information a metal hose fabricator will need in order to make an assembly for your
application. If you need assistance determining this information, we have also included an explanation
of how to analyze the application and make the appropriate selections.

In order to produce an assembly, the fabricator will need answer to the following five
questions.
1. Hose (type, alloy, and size): page 4-18
2. Fittings (type, alloy, and size for each end): pages 19-21
3. Length of the Assembly (either overall length or live length): page 22-24
4. Fabrication Options: page25
5. Accessories: page 28
If you have the answers to these questions, a metal hose fabricator will be able to make your
custom assembly. If you do not have the answers to all five questions, you will need to obtain
them. The next section (S.T.A.M.P.E.D.) is designed to help you obtain the information
necessary to determine the answers.
S.T.A.M.P.E.D
To properly design a metal hose assembly for a particular application, the following design
parameters must be determined. To help remember them, they have been arranged to form the
acronym "S.T.A.M.P.E.D."
1. SIZE
The diameter of the connections to which the assembly will be installed is needed to provide a proper fit.
This information is required
2. TEMPERATURE
As the temperature to which the assembly is exposed (internally and externally) increases, the strength of
the assembly's components decreases. Also, the coldest temperature to which the hose will be exposad
can affect the assembly procedure and/or fitting materials. If you do not provide this information, it will be
assumed that the temperatures are 70 degree F.
3. APPLICATION
This refers to the configuration in which the assembly is installed. This includes both the dimensions of
the assembly, as well as the details any movement that the assembly will experience. This information
is necessary to determine assembly length and required flexibility.
4. MEDIA
Identify all chemlcats to which the assembly will be exposed, both internally and externally. Ths is
important since you must be sure the assebly's components are chemically compatible with the media
going through the hose, as well as the environment in which the hose is to be installed. If no media is
given, it will be assumed that both the media and the external environment are compatible with all of the
available materials for each component.
5. PRESSURE
Identify the Internal pressure to which the assembly will be exposed. Also, determine if the pressure is
constant or if there are cycles or spikes. This information is important to determine if the assembly is
strong enough for the application. If no pressure is given it will be assumed that the pressure is low and
there are no pressure surges or spikes.
6. END FITTINGS
Identify the necessary end fittings. This is required since fittings for the assembly must be chosen to
properly fit the mating connections.
7. DYNAMICS
Identify the velocity at which the media will flow through the assembly. Since corrugated metal hose does
not have a smooth interior, rapid media flow can create a resonant frequency that will cause the hose to
vibrate and prematurely fail. If no velocity is given, it will be assumed that the velocity is not fast enough
to affect the assembly's performance.
|

To calculate the proper Length of a hose assembly, you need to:
1. Verify that the installation is property designed (refer to Do's & Don'ts on page 36 in
Technical section)
• Do not torque the hose
• Do not overbend the hose
• Do not compress the hose
2. Calculate the live length of the assembly· The live length of the assembly is the
amount of active (flexible) hose in an assembly; that is, the hose between the braid collars
(refer to pages 23-24 for formulas to help calculate live length for a variety of common
hose installations).
3. Calculate the overall length of the assembly - Overal length is equal to the live length
plus the lengths of the braid collars and fittings. When adding fitting lengths. be aware
that the points from wlich measurements should be taken vary lor different fitting
types. When calculcting overall length for assemblies with threaded fittings, remember
to account for the length of thread that is lost by threading into the mating connection
(refer to Thread Allowance chart on page 36 in the Technical Section).
|
JIC/SAE-type fittings measured from the
seat of the fitting
Elbows and other fittings with a radius are
measured from the centerline of the fitting
Flanges are measured from the flange face
or from the face of the stub end if one is used
Threaded fittings are measured to the end of
the fllting |
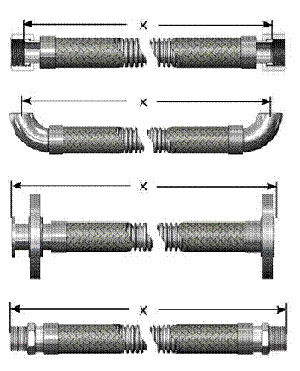 |
For the following formulas:
L _ Live length of hose (inches)
T = Travel (inches)
S = Hose outside diameter (see product data pages 9-18)
Verify that the installed radius is greater than the stated Minimum Bend Radius for
the hose at the required working pressure.
Verify that the centerline of the hose remain in the same plain during cycling to
prevent twisting the assembly.
CONSTANT RADIUS TRAVELING LOOP (A-LOOP)
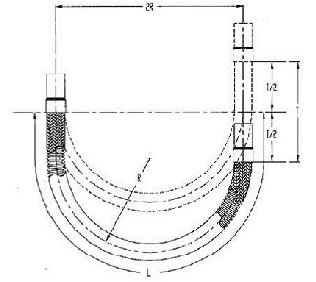
Formula: L = 4R +1/2T
VARIABLE RADIUS TRAVELING LOOP (B-LOOP)
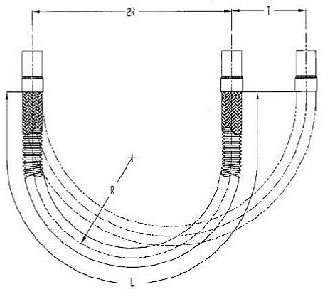
Formula: L = 4R + 1.57T |
|