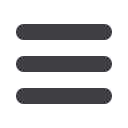
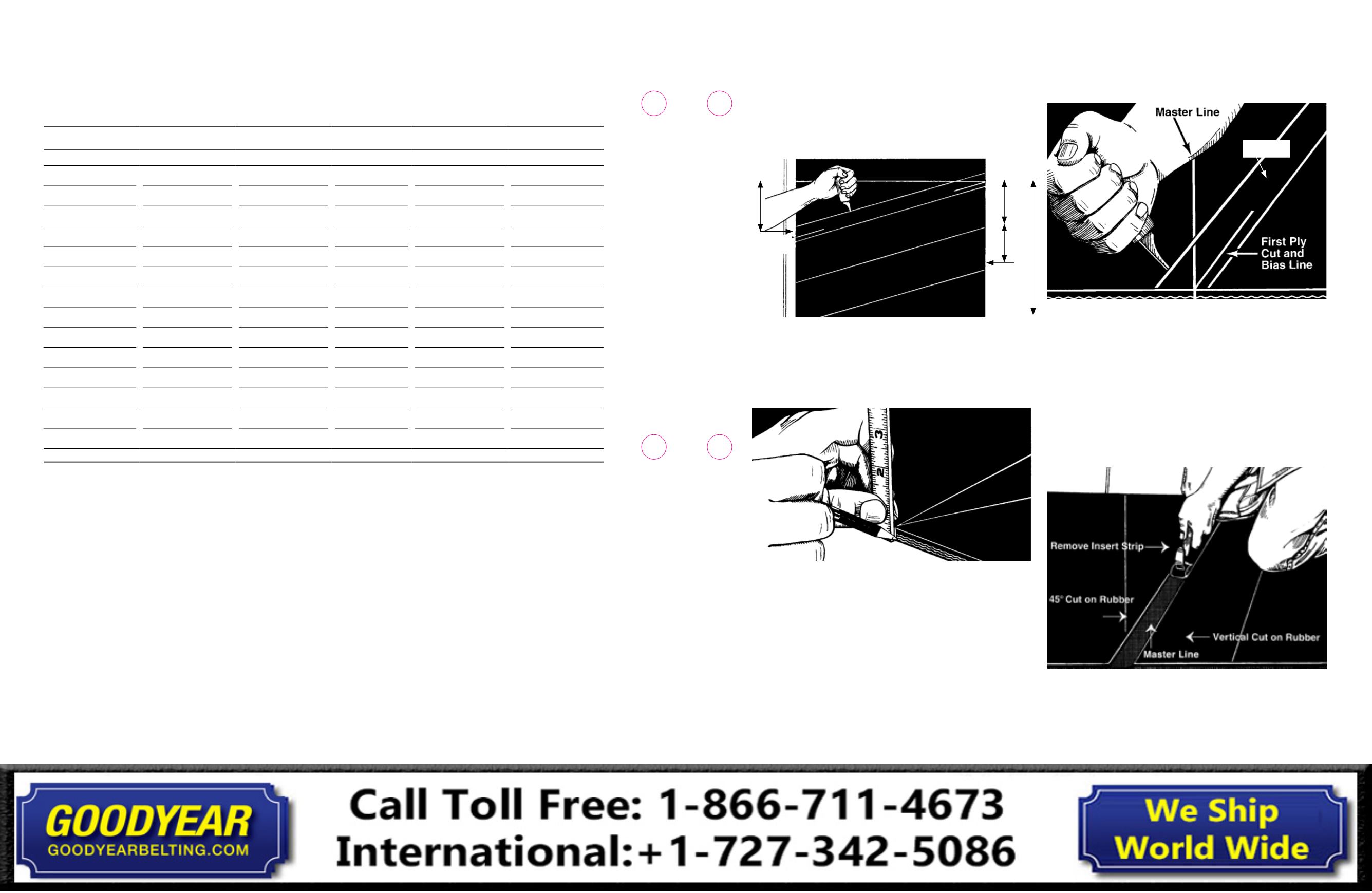
halved and the result will usually give an accurate line.
Mark the cutoff line, which is parallel to the bias line
(Fig. 11-1).
Fig. 11-1
4.
Measure off the bias length and draw the bias line to the
end of the master line on the opposite edge (Fig. 11-2). This
line marks the location of the top ply cut after the cover
gum is removed.
Figure 11-2: Marking the ply cuts down the edge of the belt.
5.
Extend the end of the bias line down over the belt edge.
6.
From the bias line measure toward the end of the belt
a distance equal to the total number of steps plus 1 in.
(25mm) trim.
7.
Lay out the cover strip for removal. Draw one line parallel
to and approximately 1/2 in. (13mm) from the bias line and
on the splice side. Draw a second line on the belt side of
the bias line but at a distance of 2 in. (50 mm) (Fig 11-3).
Figure 11-3: Showing master line and top cover insert cut lines.
Note position of the right hand and knife blade angle when cutting
45° bevel.
8.
Cut along the two covers cut lines just made. The line on
the belt side of the bias line should be skived per Fig. 11-3.
The other cut may be vertical. Do not cut too deep. If you
feel fabric, you have damaged the belt.
9.
Cut-off the belt at the cut-off line (Fig. 11-1).
10. Remove the cover strip. Note one skived cut and one
vertical cut in the cover (Fig. 11-4).
Fig. 11-4: Removing insert strip, note position of bias line, and angle cut.
11.
Connect the vertical lines marking the bias line. This will
now be the first ply cut. Using the correct ply knife, cut the
top ply along this line (Fig. 11-5).
Bias line
Bias
Step length
Step length
Plus 1" trim
Total splice length plus 1" trim
Cut-
off
line
Cover Strip
Splicing Material
1.
Solar-Shield® XL 750 splicing material will not have the
usual green tack. It is recommended to make the splice on
the bottom plate when possible. Center-line both belt ends
and secure in place.
2.
It is very important to maintain a relatively clean
work environment.
3.
Use a clean, lint-free cloth, and the specified solvent to
keep all splicing surfaces and materials clean and free of
debris. Do not saturate the carcass when cleaning. Allow
the surfaces to dry thoroughly before continuing.
4.
Specified cement is M-916-C
5.
Stir the cement thoroughly before using.
6.
Apply one even coat over the entire carcass.
7.
Spread an even layer/coat of the mixed cement to the
carcass section of the splice. Allow the cement to dry
until tacky before continuing (a slight tacky cement feel
is recommended).
8.
Wiping all rubber surfaces with solvent before use may
add some green tack. Use clean, lint-free cloth and the
specified solvent.
9.
Additional green tack may be achieved by brushing an
even layer/coat of the mixed cement to the surface of the
side of the inside rubber matching to the carcass fabric.
10. Using the specified cement between layers of the splicing
rubbers may also create better tack. Allow all cemented
surfaces to dry until tacky.
Building the Fill Strips
Cover skives are cut at a 45° angle. Use caution when cutting
the cover skives to not damage the adjacent fabric ply.
Procedure
1.
The technique for splicing fabric belts is essentially the
same for any number of plies. A 3-ply construction is
illustrated in the sketches and instructions that follow.
2.
Technical notice: For splices where the top cover rubber
gauge is 1/8 in. (3.2 mm) and greater use the reverse
cover skive on the lead end of the top cover fill strip.
3.
Measure the splice length; in addition, 1 in. (25mm) trim
starting from the end of the belt. Draw the master line.
A square and straight edge are generally used to mark
the master line on the belt as described in section 2.
In checking both edges if there is a difference, it can be
Table A-2 Curing Chart
Overall Belt Gauge
Cure Temperature
in.
mm
Decimal (in.)
Cure Time (mins.) +/- 5°F +/- 2.5°C Cure Pressure
Up to 1/8
Up to 3.1
Up to 0.125
30
325°F / 162°C
100 – 130 PIW
1/8 to 1/4
3.2 to 6.3
0.125 to 0.250
30
325°F / 162°C
100 – 130 PIW
1/4 to 3/8
6.4 to 9.25
0.250 to 0.375
30
325°F. / 162°C
100 – 130 PIW
3/8 to 1/2
9.5 to 12.7
0.375 to 0.500
30
325°F / 162°C
100 – 130 PIW
1/2 to 5/8
12.7 to 15.8
0.500 to 0.625
35
325°F / 162°C
100 – 130 PIW
5/8 to 3/4
15.8 to 19.0
0.625 to 0.750
40
325°F / 162°C
100 – 130 PIW
3/4 to 7/8
19.0 to 22.2
0.750 to 0.875
43
325°F / 162°C
100 – 130 PIW
7/8 to 1
22.2 to 25.4
0.875 to 1.000
46
325°F / 162°C
100 – 130 PIW
1 to 1
a
25.4 to 28.5
1.000 to 1.125
52
325°F / 162°C
100 – 130 PIW
1
a
to 1
e
28.5 to 31.7
1.125 to 1.250
56
325°F / 162°C
100 – 130 PIW
1
e
to 1
b
31.7 to 34.9
1.250 to 1.375
65
325°F / 162°C
100 – 130 PIW
1
b
to 1
f
34.9 to 38.1
1.375 to 1.500
70
325°F / 162°C
100 – 130 PIW
1
f
to 1
c
38.1 to 41.2
1.500 to 1.625
78
325°F / 162°C
100 – 130 PIW
1
c
to 1
g
41.2 to 44.4
1.625 to 1.750
88
325°F / 162°C
100 – 130 PIW
44
43
Conveyor Belt
Fabric Splice Manual
Conveyor Belt
Fabric Splice Manual