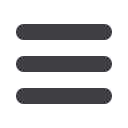
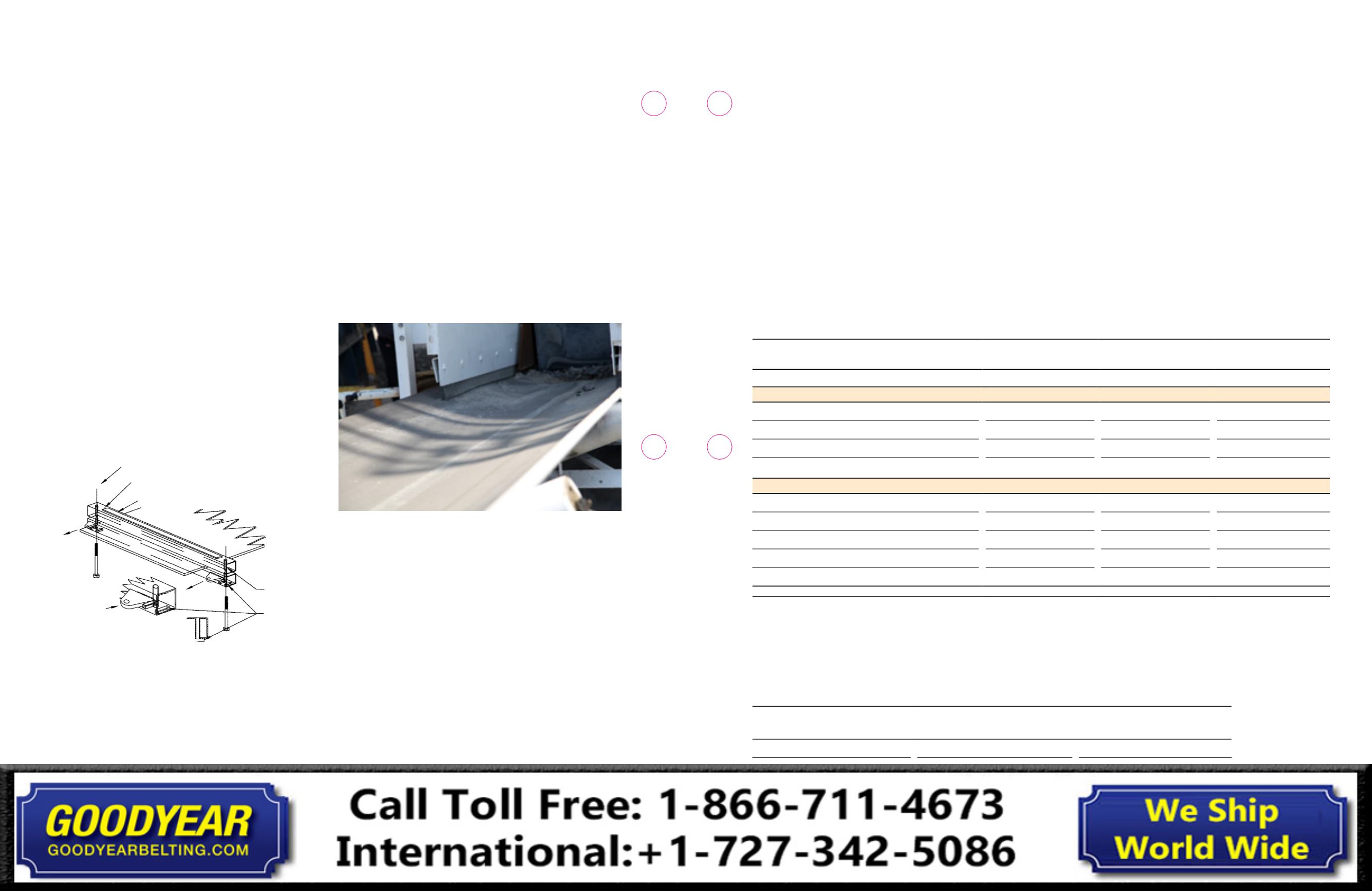
Fabric belting is usually installed so that most of the take-up
travel is available for subsequent increase in belt length.
The belt may be tensioned with a suitable take-up
device as follows:
1.
When the counterweight is on: Tie the take-up off 6 in.
to 8 in. (150mm to 200mm) above the desired running
position. (Consideration may have to be made for
excessive sag.) Next, pull the belt until the take-up starts
to lift and the tie-off ropes become slack. Make the final
splice allowing a minimum of belt slack.
2.
When the counterweight is not on: Splicing without the
counterweight installed is undesirable, however the
following procedure should be employed if necessary.
Use suitable belt clamps to hold the take-up pulley 6” to 8”
(150mm to 200mm) above the desired running position.
(Consideration may have to be made for excessive sag.)
Pull the belt to its running tension, which can only be
estimated in this situation. Judgment in estimating this
tension will improve with the experience of the splicer.
Take-Up Travel and Initial Position
Tables 2-1 and 2-2 show the recommended minimum take-up
travel and initial take-up position, respectively.
›
This table is a general guideline. See individual product
brochure for more specific data.
›
Take-up location position per Table 2-2.
›
Drive location at or near the high-tension end of the conveyor.
›
Only short feeder belts and similar would normally be
vulcanized on conveyors with a manual take-up.
+ Take up conditions and travel amounts shown in Table 2-1.
Table 2-2 Recommended Initial Take-Up Position +
Carcass Material (Warp)
Percent Available For
Length Increase
Percent Available For
Length Decrease
Steel
25%
20%
Nylon, Polyester, Aramid, Fiberglass
90%
10%
If calculating in S.I. units, multiply the belt weight (kg/m)
times the vertical lift and add 10%. For example, assume
a 60-kg/m belt and a 100 m high slope. The approximate
pull is (60 x 100) x 1.1 = 6600kg.
If the conveying side and the return side have been fed on
separately, the final splice can be made at the bottom of the
slope where the ends of the belt meet. In some situations, it is
advisable to use a suitable temporary splice to index the belt
and complete the final splice at the original location. Making the
final splice at the top of the slope is possible but a greater force
will be required to remove the sag and lift the counterweight.
Belt clamps must be used on the final pull. The system
illustrated in Fig. 2-6 will avoid dismantling the work area by
allowing a suitable length of belt to lie back over the clamp.
Tensioning the Belt
Once the belt has been pulled onto the conveyor system,
it must be tensioned before splicing to facilitate correct
positioning of the take-up and to eliminate sag. The tensioning
operation takes place at the location where the last splice will
be made. After final tensioning, clamps are placed on each
end of the belt. These are made of steel and have a clamping
surface as indicated in Fig. 2-6.
Tension is applied by means of a power device which is used to
pretension the belt before “clamping off.”
When tension measuring load cells or scales are used, they
are rigged to measure the pull on the take-up pulley. The belt
is pulled until the load cell or scales register a tension equal to
or slightly greater than the recommended take-up force. Make
allowance for an amount of belt necessary to correctly position
the counterweight from this point.
Certain basic statements and recommendations can be made
about tensioning for splicing:
1.
Belts, which are tensioned by pulling in only one direction,
require more splicing tension than those pulled in both
directions.
2.
Belts spliced at the top of the slope require more tension
while splicing than those spliced at the bottom.
3.
Slope belts having an anti-rollback device, which cannot be
released, must be tensioned by pulling in the direction of
belt travel only.
4.
Check the belt frequently during tensioning to ensure that
the belt is free and not binding at any place.
5.
During the final tensioning pull, be sure the ends of the belt
are lined up properly.
Conveyor installations having limited take-up travel should be
spliced to a tension based on the loaded running tension. This
tension should be specified by Continental ContiTech. and
measured by suitable load cells or dynamometers. Where it
is practical, fabric belts should be run for several weeks with
mechanical fasteners before making the final vulcanized splice.
Obtaining the required tension depends heavily on the
experience of the individual making the splice. It is possible for
a gravity-type take-up to damage the conveyor structure if it is
positioned too close to the forward or upward stop. Too much
tension applied to a relatively short belt may thus have a harmful
effect on the pulley shafts and bearings as well as the belt.
Grade 8 Bolts – 1 in. to 1¼ in. – Hard Nuts and Washers
Weld 1/2" x 2" Flat Bar to Tube to Bow Slightly
Square Tubing – min. 1/4 in. wall – A-53
Adequate plate,
eye and shackle
for load
Detail of Square Tube
End Typical grind the
weld on the round tube
flush with the square tube
Internal Sleeve
so tube doesn’t
crush
Weld Keystock
position to
prevent bolt
turning
Fig. 2-6: Tension Clamp for Splicing
8
7
Conveyor Belt
Fabric Splice Manual
Table 2-1 Recommended Minimum Take-Up Travel In Percent Of Center Distance
Type Of Take-Up And Carcass Material (Warp)
Percent Of Rated Tension
100%
75%
50%
Manual Take-Up
Nylon
4.0%
3.0%
2.0%
Polyester
2.5%
2.0%
1.5%
Aramid
2.0%
1.5%
1.0%
Fiberglass
1.0%
0.75%
0.5%
Automatic Take-Up
Nylon
3.0%
2.50%
1.50%
Polyester
1.7%
1.25%
0.75%
Aramid
1.5%
1.0%
0.75%
Fiberglass
0.5%
0.4%
0.25%
Steel
0.3%
0.23%
0.15%
Conveyor Belt
Fabric Splice Manual