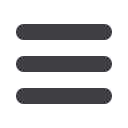
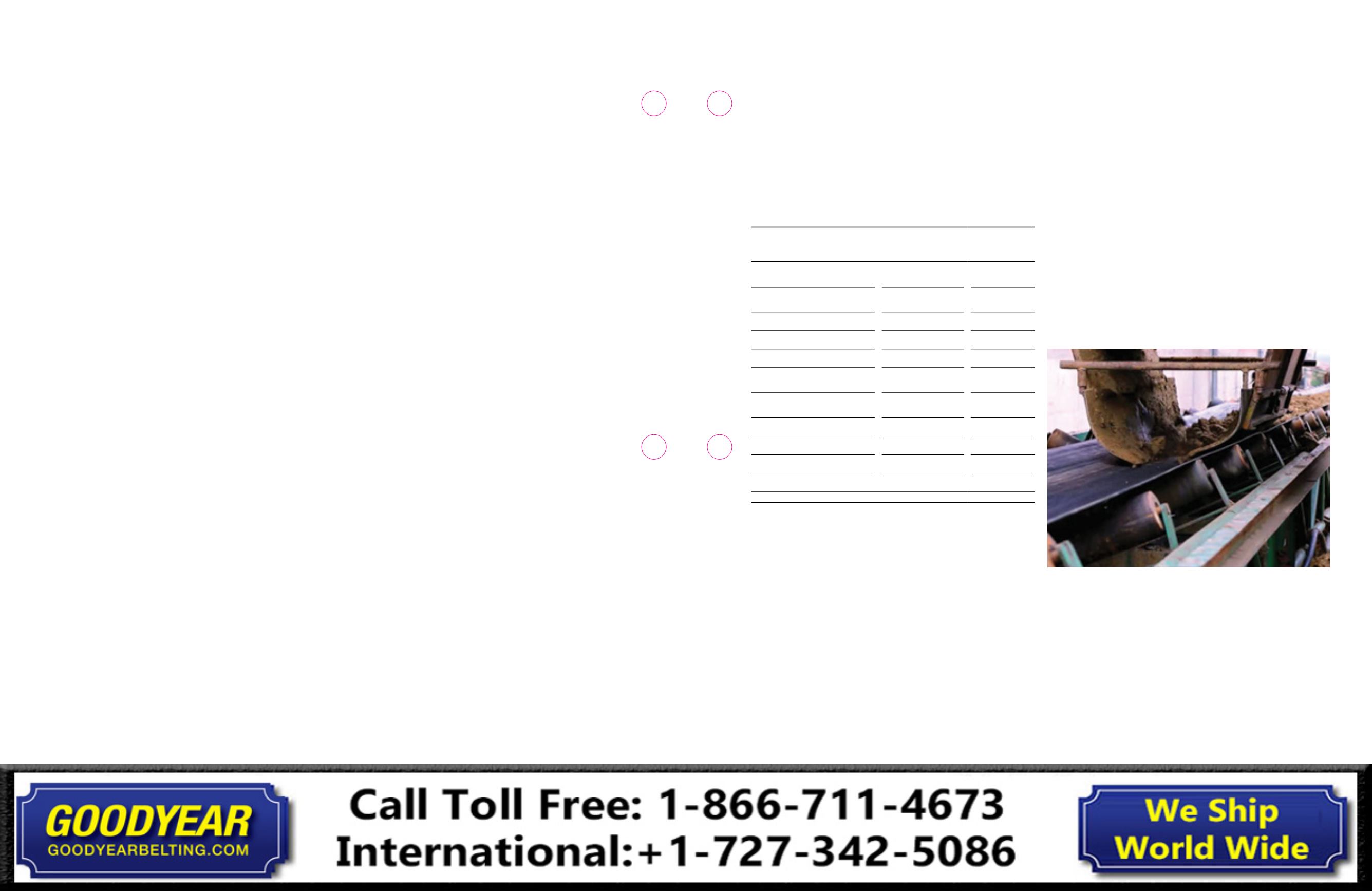
7.
Do handle splice materials in accordance with all federal,
state and local laws. Become familiar with MSDSs for
all materials.
8.
Do use only the specified materials for the belt to be spliced.
9.
Do not use splice materials that are beyond their
shelf life/age limits.
10. Do not store splice rubber in direct sunlight or heat.
Most Common Fabric Splice Mistakes
(That Lead to Premature Splice Failure)
1.
Over Cure or Under Cure
of splice rubber resulting
from improperly controlled platen temperatures.
Continental ContiTech specifies a minimum of one
thermocouple per heating element used.
2.
Nicking or cutting the fabric plies,
thereby damaging the
warp and fill cords.
3.
Buffing the fabric.
Do not directly buff the fabric surfaces.
4.
Curing the splice with wet cement
can cause ply and/or
cover blows
5.
Over prodding the fabric
when lifting the plies will
damage the warp and fill cords.
6.
Reducing the specified step lengths
of the splice to fit
into a short vulcanizer or to save time will significantly
reduce the vulcanized splice strength.
7.
Assembling a splice with contamination
can reduce ply
and cover adhesion/bonding.
8.
Using over age, incorrect or improperly stored materials
can significantly reduce ply and cover adhesions.
9.
Using incorrect compounds and/or cements
can
significantly reduce adhesions as well as cause ply and
cover blows.
10. Improper splice alignment
can cause off-center tracking.
11. Overlapping and/or misaligned plies and/or carcass
fingers:
Align the splice with a gap of approximately
0.063 in. (1.6 mm) at ply seam/joint and between fingers.
Fill the gaps with the specified inside rubber.
Proper Storage, Handling and Use of Splice Materials
1.
It is the responsibility of the splicing company and/or the
end user/customer to properly store and handle all splice
materials. It is also their responsibility to dispose of any
unused or unwanted materials properly.
2.
Material shelf life may be extended if stored in a
refrigerated storage area.
3.
Each material will have the Refrigerated and Non-
refrigerated date posted on them.
4.
Do not use splice materials that have exceeded their
shelf life/expiration dates.
5.
Keep all splice rubber completely wrapped with film/poly.
6.
All splice materials must maintain identification and
expiration periods attached.
7.
Non-refrigerated splice materials must be kept away
from and out of direct sunlight and heat.
8.
All splice materials must be stored in a clean, dry and
cool environment.
9.
Do not store splice material near electrical motors or in a
possible wet environment.
10. Avoid condensation of materials immediately before use.
11.
Avoid repeatedly handling open splice rubbers with
dirty/oily gloves and/or hands.
12. Wipe all rubber surfaces with a clean, lint-free cloth and
the specified solvent.
13. Roll all rubber sheets in place using a flat roller and a
porcupine roller.
Curing Rules
1.
Never shorten the splice to fit into a vulcanizer without
the approval of the belt manufacturer.
2.
Be certain the vulcanizer can meet the specified cure time
temperature and pressure throughout the cure cycle.
3.
Use a minimum of one thermocouple per heating
element/zone.
4.
Follow the belt manufacturer’s specified cure time, cure
temperature and cure pressure.
5.
Use steel or aluminum edge guides against the edges of
the splice and adjacent belt ends. The edge guides are to
be approximately 1/16 in. less gauge than the belt gauge
(not the splice gauge).
6.
Use steel or aluminum guides thinner than the edge
guides as balance guides.
7.
Cool the finished splice and platens to at least 130°F
(54°C) or lower before releasing pressure.
8.
Do not leave the finished splice on a hot platen.
9.
Buff all fill strip rubber overflow for a smooth, even
transition from the belt to the splice.
50% Rule – Be Here Now – In Case of Power Failure
1.
It is very important that someone is watching over the
vulcanizer and documenting the cure time, the cure
temperature from each thermocouple and the cure
pressure at given intervals throughout the cure cycle.
2.
In case of a power failure while curing the splice, do not
release or lower the curing pressure, but hold it until
power is restored and then bring the vulcanizer back
to cure temperature. At that time:
›
If the splice had less than half its specified cure time
before the power failure, repeat the entire splice.
›
If the splice had cured one half or more than the
specified cure time, then finish curing the remaining
time after all the thermocouples again register the
specified cure temperature.
3.
If the vulcanizing pressure is lost on the surface of the
splice, the splice must be remade.
Splicing Rules
1.
Follow the specified dimensions for the splice.
2.
Never change or alter the splice dimensions without
the approval of the belt manufacturer.
3.
Use only the compatible specified splice materials.
4.
Cure according to the belt manufacturer’s specifications.
5.
Follow the belt manufacturer’s established best practices
for splicing.
6.
Document each splice including the splice materials used
and their expiration dates.
Splice Materials - Do’s and Don’ts,
Age Limits
1.
Do stir cements thoroughly before and during use.
Cements that have jelled or remain jelled/settled out
after stirring are not to be used.
2.
Do keep cans of cement tightly sealed and stored in
a cool dry area. Refrigeration of some cements are
recommended. See chart on page 4. Recommended
refrigeration temperature of 45°F to 55°F (7°C to 12°).
Avoid freezing cements.
3.
Do keep uncured splice rubber clean, sticky and protected
by film/poly. Use the specified solvent to wash uncured
rubber surfaces before use.
4.
Do minimize handling of clean splice rubber and fabrics.
5.
Do permit refrigerated splice materials to come to or
near the ambient temperature before using to avoid
condensation on exposed surfaces.
6.
Do permit solvent-washed and/or cemented surfaces
to dry until tacky before use.
4
3
Conveyor Belt
Fabric Splice Manual
Age Limits
Unrefrigerated
(But Cool and Dry)
Refrigerated
All Rubber and Breakers Except
Solar-Shield® XL 750
6 Months
12 Months
Solar-Shield® XL 750 Rubber
and Coated Breakers
3 Months
6 Months
M-856-C Cement
3 Months
6 Months
M-924-C Cement
3 Months
6 Months
M-1200-C Additive Cement
6 Months
12 Months
VTI-600-FC Cement/Fabric
Belt Splices
18 Months
N/A
VTI-900-SCC Cement/Steel
Cable Splices
18 Months
N/A
M-750-C Cement
6 Months
12 Months
M-916-C Cement
6 Months
12 Months
M-918-C Cement
6 Months
12 Months
M-920- C Cement
6 Months
12 Months
Conveyor Belt
Fabric Splice Manual