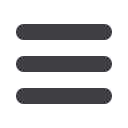
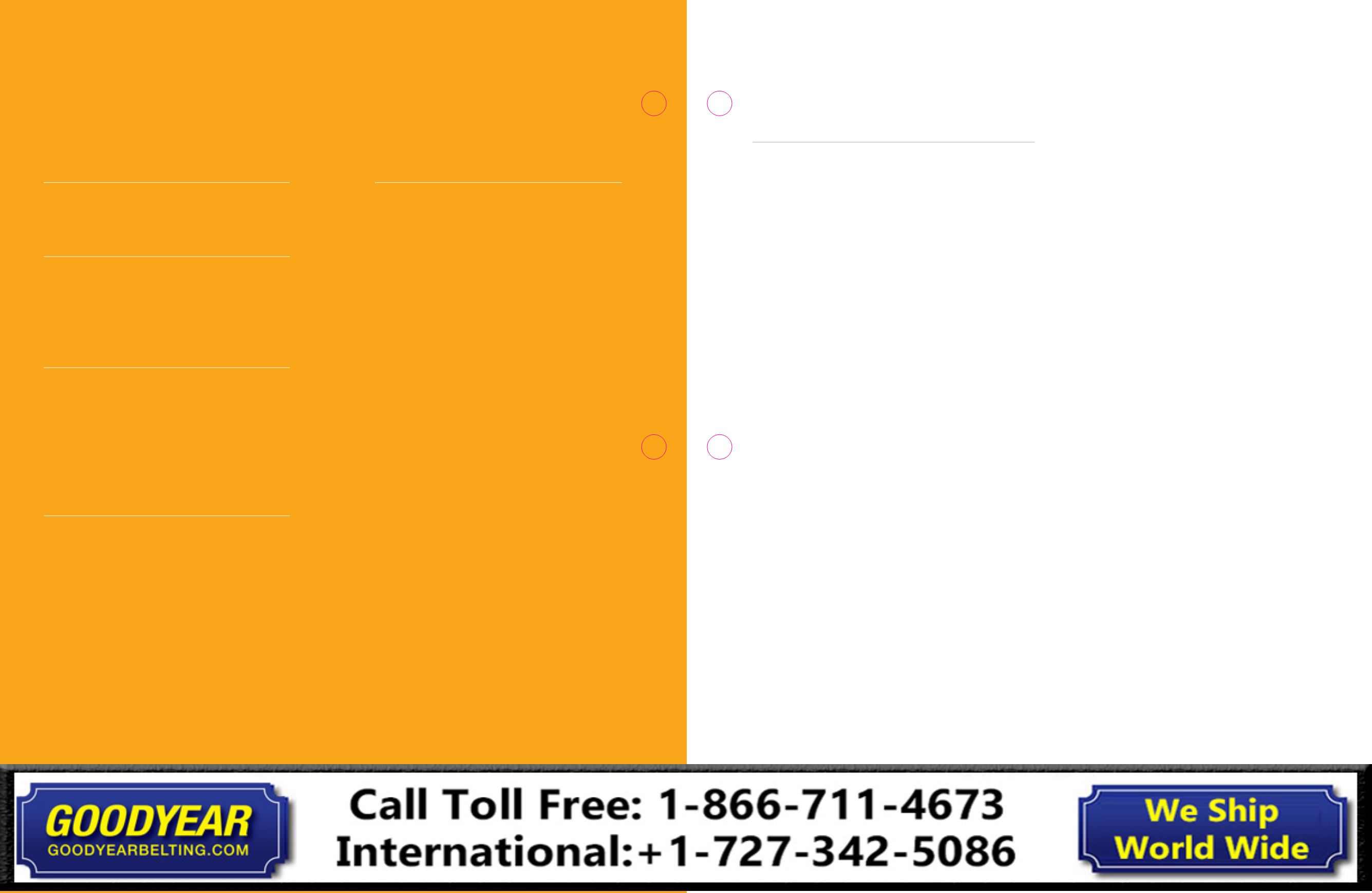
I. Splice Technologies
Splicing Best Practices
White Dot Procedure
1.
The White Dot Procedure is a method to identify the
“Factory Cut Edges” of narrow belts that are slit from
wider belts.
2.
On rare occasions the narrow belts may camber or bow
towards the Factory Cut Edge side of the slit belts.
3.
The Factory Cut Edges are clearly marked and identified
from the factory before shipping the belt.
4.
The words “Factory Edge” are spray painted on the side
of the belt.
5.
When the narrow slit belts are being spliced together on
the same conveyor, the Factory Cut Edges must be aligned
on the same side of the conveyor.
6.
To match the Factory Cut Edges on the same side of the
conveyor, one of the narrow slit belts must be re-rolled.
This belt will have the “Factory Edge” side marked as well
as “Re-Rolled” spray painted on the other side of the belt.
7.
Many times belts that bow/camber can run straight on the
system after initiating belt tension and running the belt for
a break-in period. However, some belts that bow/camber
may be difficult/impossible to train and run straight on
the system without matching up the “Factory Cut Edge”
sides on the same side of the conveyor system.
Building the Fill Strips
1.
A leading cause of fabric belt premature splice failures is
the breakdown of the fill strips.
2.
The typical specified cover skive is 4 in. at the base
x full width.
3.
Cover rubber skives are cut at 45° angles. Buff the cover
skives and approximately one inch of the surrounding
belt cover.
4.
Remove all buffing debris from the splice area.
5.
Using a clean, lint-free cloth, wipe the 45° cover skives and
the buffed surrounding rubber with the specified solvent.
6.
The ply seam/joints must have a 1/32 in. to 1/16 in. gap.
Do not butt the fabric plies tight or allow them to overlap.
7.
Apply one even layer/coat of the specified cement to the
exposed fabric only. Do not cement the 45° cover skives.
8.
Allow the cement to dry until tacky. Do not allow the
cement to dry past the tacky stage.
NOTICE: Continental ContiTech does not typically specify cementing
rubber to rubber interfaces. Testing has proved the best rubber to
rubber bonding is achieved by wiping with the specified solvent.
However, for those rare occasions when additional green tack is
needed, apply a layer/coat of the specified cement to the
rubber surfaces.
9.
Place a noodle or narrow strip of the inside rubber over
the ply seam/joint.
10. Apply a sheet of the specified inside rubber over the fabric
surface only. Do not allow the inside rubber to advance
onto or over the 45° cover skives.
11.
Using a porcupine roller, roll the sheet of inside rubber
flat and remove all possible trapped air.
12. Using a clean, lint-free cloth and the specified solvent, wipe
the top surface of the freshly installed inside rubber sheet.
13. Using a clean, lint-free cloth and the specified solvent, wipe
the bottom surface of the specified breaker.
14. Apply the breaker over the ply seam/joint. Carefully center
the breaker so that equal lengths are positioned on each
side of the ply seam/joint.
15. The breaker is approximately 3.5 in. x full width. This will
allow approximately 1/4 in. of space from each edge of
the breaker to the base of the 45° cover skive.
16. Do not allow the breaker to advance to the 45° cover skive.
17.
Using a porcupine roller, roll the breaker flat and remove
all possible trapped air.
18. Using a clean, lint-free cloth and the specified solvent,
wipe the top surface of the breaker and the bottom of
the specified cover rubber.
19. Install the cover rubber. Be sure of a tight fit against
the 45° cover skives.
20. Using an awl, puncture holes throughout the cover
rubber insert.
21. Using a small straight edge verify that there is sufficient
rubber in the fill strip area to prevent low pressure.
Ply Seam Gaps
1.
All ply seams must have a gap measuring approximately
1/32 in. to 1/16 in. wide.
2.
Never butt the ply seams/joints tight together.
3.
Never allow the ply seams/joints to overlap.
4.
Place a noodle or narrow strip of inside rubber over the
ply seams/joints.
5.
Each ply seam/joint must be properly aligned using steps
#1 - #3 when dry fitting the splice.
2
Table of Contents
I. Splice Technologies
Splicing Best Practices
2
Splice Materials - Do’s and Don’ts, Age Limits
3
Most Common Fabric Splice Mistakes
4
II. Belt Installation
Belt Storage and Installation
5
Handling the Roll of Conveyor Belt
5
Stringing the Belt
6
Tensioning the Belt
7
Take-Up Travel and Initial Position
8
Cutting the Belt to Length
9
III. Fabric Splice Preparation
Preparation of Work Area
10
Splice Tools
11
Direction of Splice and Bias
13
Existing Splices Loaded onto a Conveyor System
14
Establishing a Master Line
14
Establishing a Center Line
15
Dry Fit Splice Alignment
15
Addressing Belts with Damaged Edge(s)
15
Addressing Belts with Unequal Widths
15
IV. Vulcanizing
Cure Time and Temperature
16
Pressure
16
Power Failure: 50% Rule
17
Pressure Failure
17
Vulcanizing the Splice
17
Press Platen Cooling
18
Splice Completion
18
General Curing Notes
18
V. Belt Splicing Procedures
Fabric Belt Bias Step Splice
19
Splice Dimensions
19
Splice Bias
19
Procedures
19
Bias Step Finger Splice
26
Long Life Full Carcass Finger Splice
29
ContiPipe™ Belt Splicing
34
Mechanical Splice (Fasteners)
36
Squaring the Belt End
36
Classes of Mechanical Fasteners
36
Tightening Fasteners
37
Hazard to the Belt
37
Fasteners for Special Requirements
37
Fastener Application Cover Skive Instruction
38
Elevator Belt Splice
40
Installation
40
Splicing
40
Attaching Buckets
41
Solar-Shield® XL 750 Splicing
42
Splice Dimensions
42
Splice Bias
42
Step Length/Curing Chart
42
Splicing Material
43
Building the Fill Strips
43
Procedure
43
Special Belt Splices
48
Wedge-Grip
48
Bareback
48
Cleated Belt
48
Fold Belt 600 2 Ply
49
Conveyor Belt
Fabric Splice Manual