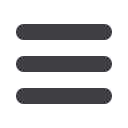
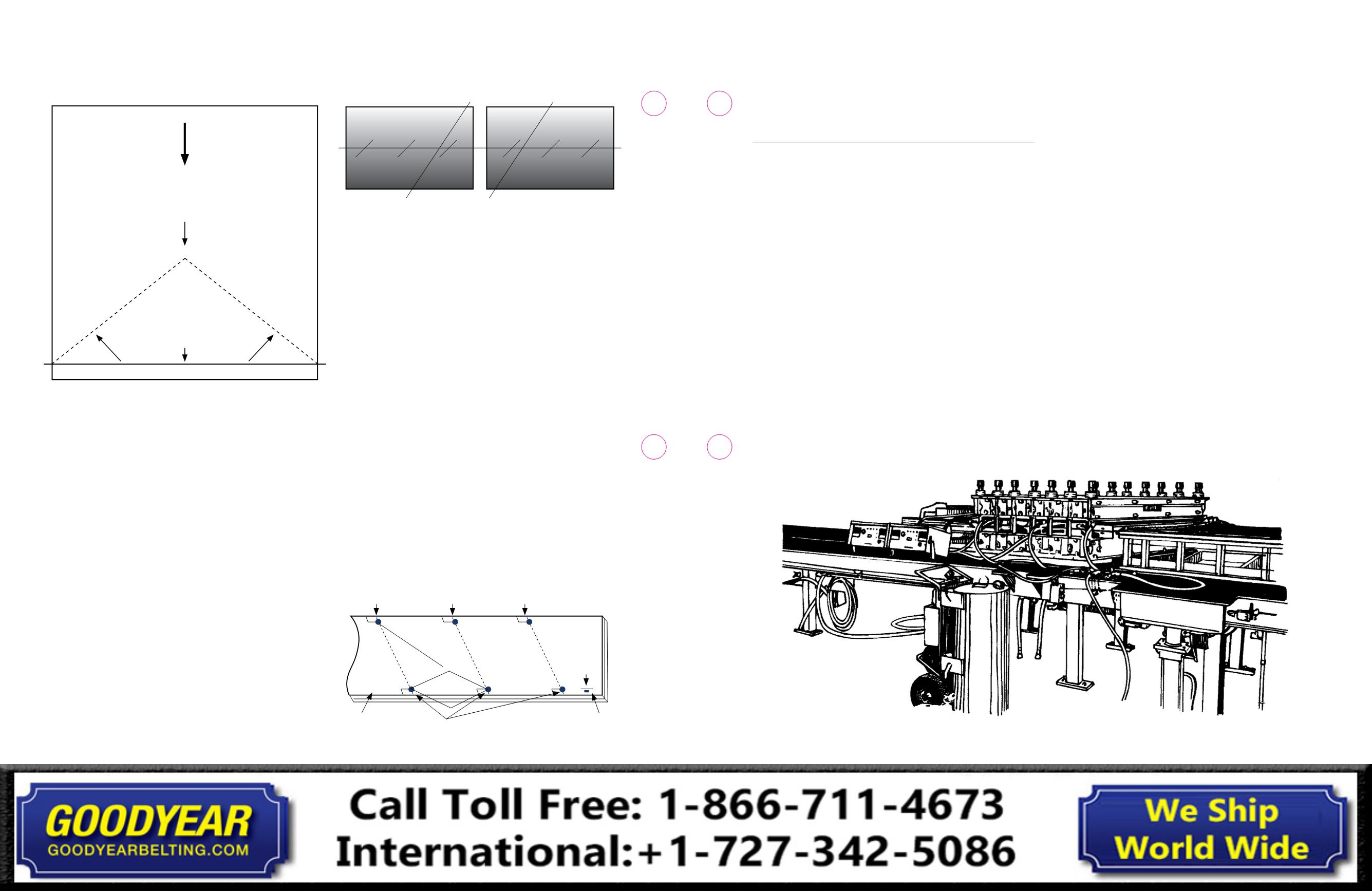
Fig. 4-1
IV. Vulcanizing
Cure Time and Temperature
Follow the belt manufacturer’s specified/recommended curing
rules. Using the correct time and temperature will ensure the
ultimate cure for the splice rubber. Altering or changing the
cure time and/or cure temperature may jeopardize the integrity
of the splice.
The cure time and temperature shall be monitored and
documented at defined intervals throughout the splice cure
and cool down. Use thermocouples to accurately monitor the
core temperature. Control the platen temperatures to achieve
the specified cure temperature by adjusting the set points on
the power control box. The temperature reading displayed on
the thermocouple is the accurate cure temperature during
the cure cycle. Use a minimum of one thermocouple per
heating element.
Pressure
The use of a field vulcanizer with a bladder(s) to apply pressure
to the entire platen surface is preferred because of its uniform
pressure distribution (Fig. 4-1). If multiple bladders are used,
they must be connected to a common manifold to ensure
equal pressure in all bladders.
Other types of pressure systems on field vulcanizers are
acceptable if they are capable of meeting a tolerance of +/- 5%
over the curing area of the platen. During the cure cycle on
bladder presses, pressure should be monitored using
a transducer connected to a suitable recording device.
1.
Follow operating and safety procedures recommended
by the vulcanizer manufacturer.
2.
Use care if pressure is applied while the vulcanizer
is still cold. Platens can expand when heated causing
extreme pressures, which may damage the vulcanizer.
3.
To obtain edge pressure, use steel guides along each
edge which are approximately 1/32 in. – 1/16 in.
(0.8mm - 1.6mm) less than belt thickness. The guides
should be drawn together against the edges as
uniformly as possible with ratchet chain type or cord
type come-along. These come-alongs should be only
drawn up snug initially. Then, after the vulcanizer
pressure is applied, they should be drawn tight.
4.
Use of wedges against the edge irons in the splice
area will limit bowing.
5.
The recommended vulcanizer pressure for fabric
belts is 100-130 psi (.69 - .89 MPa), however precautions
should be taken NOT to exceed the vulcanizer
manufacturer’s maximum pressure.
Fig 3-10: Swinging Arc Method
Establishing a Center Line
(Fig. 3-11)
1.
Center-lining the belt ends is necessary to ensure a
properly aligned splice.
2.
Place the belt ends on the bottom platens so that the
distance between the top of the 45° cover skives equals
the splice length.
3.
The center of the splice should be positioned on the
center of the bottom platen (both length and width).
4.
The press platens must be
a minimum of four inches
longer and wider than the completed splice.
5.
On each belt end mark four evenly spaced center
locations from the 45° cover skives to the end of the
work table.
6.
Extend a string from the marks at the outside ends of
each work table, supported by a suitable block to keep
the string free from interference by the belt surface.
7.
Use a square to align these end marks to the string.
8.
Check the remaining center marks and adjust the belt as
necessary until all marks are aligned.
9.
Verify the splice length distance between the 45°
cover skives.
10. Secure the belt ends in this position. Typically
C-clamps are used to secure the belt to the work table.
11.
Nail blocks of wood to the table flush with the belt edges
to prevent lateral movement.
12. Cover the bottom and top of the splice with release paper.
Center mark
Equal distances
Master line
Fig. 3-11
Dry Fit Splice Alignment
1.
Once the center line procedure is satisfactorily completed
and the belt ends are firmly clamped stationary, it is
necessary to verify the alignment of each ply seam/joint
before building the splice.
2.
The ply seams/joints must have a 1/16 in. gap approximately.
3.
Ply seams must not be butted or overlapped.
4.
Carefully trim the ply seams if needed. Use caution not to
damage adjacent plies.
Addressing Belts with Damaged Edge(s)
1.
When belt edges are damaged it is necessary to establish a
master line on one end only by one of the above methods
and proceed to step that end down.
2.
Lay the ends together, align by eye as well as possible, and
transfer all marks to the second end.
Addressing Belts with Unequal Widths
(Fig. 3-12)
1.
If the two belt ends are not the same width then the wide
end is to have bias and step points marked along the
edges in the normal manner.
2.
Then measure in from these marks at right angles to the
edge a distance half the width difference and make marks.
3.
Connect these new marks for correct bias and step lines.
Splice Areas
Fig. 3-12: Addressing Belts with Unequal Widths
1.
Place the initial bias and step marks at the edges of the wider belt but
do not draw the line across the belt width.
2.
Then measure at right angles from the edges at these initial
marks and establish new points one-half the width difference
of the two belts.
Half of the belt’s width difference
Right angles
Wider of the two belts
Wider belt bias and step points.
16
15
Conveyor Belt
Fabric Splice Manual
Conveyor Belt
Fabric Splice Manual