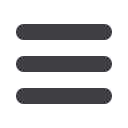
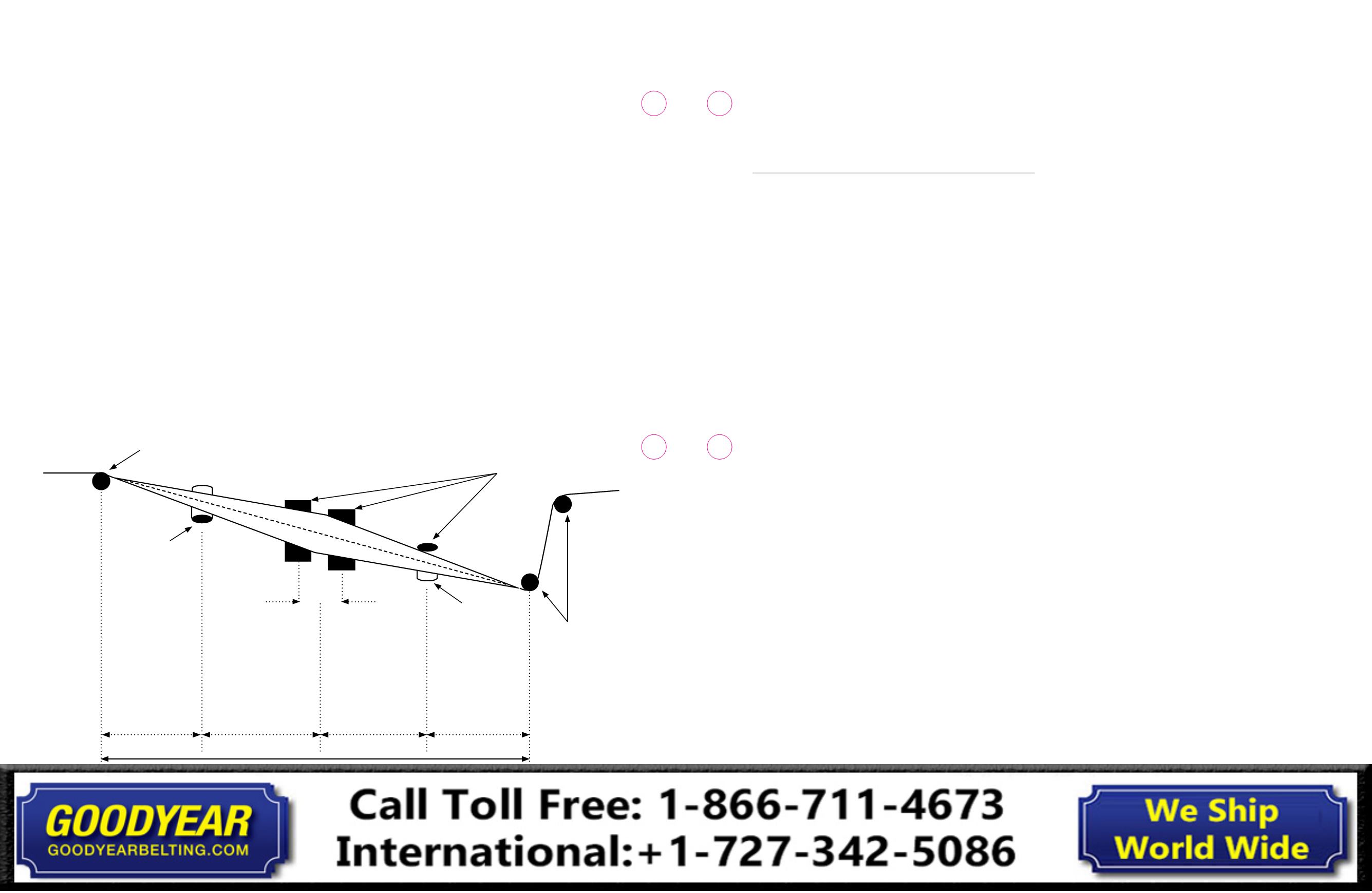
III. Fabric Splice
Preparation
General
First one must verify the type of splice required for the belt
being spliced.
Preparation of Work Area
1.
Preparation of the work area is one of the most critical
items while performing any splice. Care should be taken
during the selection of the work area with due regard to
safety and ease of egress.
2.
Often, time “saved” during the set-up of the work
area is lost due to poor splice quality associated with
misalignment, cluttered working areas, or unsafe
working areas.
3.
Selecting the best working area and scheduling the
necessary time to set up and prepare the area will often
result in better workmanship.
Location for Splice Work
1.
On incline or decline belts, it is desirable to work at the
lower end if possible. Splices can be made at the upper
end, but high belt tensions can cause difficulties in
restraining the belt with clamping devices.
2.
At the upper end, there is a risk of the belt breaking away from
the clamps and running loose down the slope.
3.
Level belts may be spliced at any location where power is
available and it is convenient to set up the equipment.
4.
The location must have facilities for hoisting the vulcanizer
or other heavy equipment and placing them in the
desired positions.
5.
The locations must be long enough and wide enough
to accommodate the necessary work area and shelter. See
Shelter For Work Area below.
6.
One must account for the weight of splicing, personnel and
ancillary equipment if the splicing is to be completed on
the conveyor structure.
7.
When splicing at elevated areas, it may be required to wear
a safety harness to prevent accidental falls.
Shelter for Work Area
1.
A shelter must be constructed over the splice area
to keep the belt ends clean and dry at all times.
2.
In hot weather, the cemented belt ends must never
be exposed to direct sunrays.
3.
In cold weather, the shelter must be heated to 60°F
(16°C) minimum.
4.
The size of the shelter depends on the width and
construction of the belt to be spliced. Generally it should
be 4 ft. to 6 ft. (1.2m to 2.0m) wider than the belt, 12 to
18 ft. (3.6m to 5.5m) longer than the splice and have 8 ft.
(2.4m) or more between roof and the work table.
5.
As a rule of thumb, 4.5 times the splice length is a good
starting point.
6.
The splicing company is typically responsible for
constructing the shelter and maintaining a clean
and contaminant-free splice.
7.
If a permanent building is not available, then a temporary
shelter must be built to protect the exposed belt ends
from adverse weather conditions, dust, and all other
forms of contamination.
Temperature and Humidity for the Work Shelter
1.
It is recommended that the temperature in the work area
be maintained at 60°F (16°C) or greater.
2.
It is also recommended that the relative humidity be
less than 75%.
3.
This is to ensure that the rubber materials to be handled
will be both tacky and flexible.
4.
In hot, humid conditions this will also help to prevent
condensation while maintaining equal drying time for
surfaces coated with the specified cement and/or solvent.
5.
These guidelines are to ensure the splice rubber materials
remain tacky and flexible. Controlling the humidity in the
splice shelter may be difficult or impossible at times.
6.
Avoid condensation of the cements and splicing rubber.
7.
When splicing during colder weather, allow the cements
and splicing rubber to warm beyond the possible
condensation state.
8.
When splicing during extreme hot ambient temperatures,
avoid handling/touching the open belt ends, the exposed
fabric carcass and splicing materials with bare hands as
sweat and/or oils may transfer and contaminate the fabric
carcass and splicing materials.
9.
Avoid all types of moisture such as rain, water, sweat or
other non-specified liquids from contacting the open belt
ends, the exposed fabric carcass and splicing materials
10. Open-flame torpedo-style kerosene heaters are not
recommended due to explosive hazards and potential
contamination by residual kerosene in the splice area.
11.
Maintain a clean and orderly shelter. Never walk on belt
where covers have been removed or fabric is exposed.
Cutting the Belt to Length
1.
When splicing a belt to a specified length or a net endless
length (NEL), the following total length of belt will be
required: The specified NEL length plus the bias length,
plus one splice length, plus a minimum of 2 in. (50mm)
trim allowance. If two or more belt rolls are to be spliced
NEL, add a splice length plus a minimum of 2 in. (50mm)
trim for each roll or splice.
2.
When replacing a damaged section of belt the required
length of new belt will be: The length of the damaged
section plus 2 splice lengths, plus a minimum of 4 in.
(100 mm) trim allowance. Cut the ends square.
NOTE: Whenever a section of new belt is to be spliced into an old belt
the length of old belt to be removed should include as many of the old
splices as is reasonably possible.
3.
On very short conveyors, it is sometimes necessary to
remove the tail pulley in order to have adequate slack
for splicing after cutting to length.
4.
When a splice has to be done on the return run,
precautions must be used in measuring the belt length.
The splice area may be located on the ground requiring
an adjustment in belt length, if the conveyor is elevated
above ground level.
5.
In most cases, it is not possible to pull up and use the
entire belt that appears to be available in a take-up. About
4 ft. (1.2m) of belt will be needed for slack in splicing. In
other words, for a re-splice the take-up should have at least
a splice length plus 4 ft. (1.2m) available for removal.
6.
If a fabric splice is to be remade and there is very little belt
in the take-up, the old splice can be cut parallel to the bias
and near the center. The old splice area is then re-stepped
and re-spliced and the take-up is only raised half of the
total length of the steps on one end of the splice.
7.
Belts running on 45° idlers on a system with a minimum
take-up should be clamped off at or near the head pulley.
Tension the belt with a center pulling plate so the belt will
conform to the idlers when pulled and then mark master
line on each end. Leave minimum slack for the vulcanizer.
CAUTION: TURNOVERS: THE CONVEYOR PROFILE MUST
BE CONSIDERED WHEN STRINGING THE BELT TO PREVENT
THE FINAL ORIENTATION FROM BEING UPSIDE DOWN.
FOR EXAMPLE, TURNOVERS ADD A TWIST TO THE BELT
THAT MUST BE ANTICIPATED. CONTINENTAL CONTITECH
RECOMMENDS TURNING THE BELT 180° AT THE HEAD AND
REVERSED 180° AT THE TAIL.
SEE FIG. 2-7 FOR A TYPICAL TURNOVER DESIGN.
Fig. 2-7: Turnover Design 42 in. wide 1500 PIW
24" Dia
45 Deg
Pulleys
16" Dia
24" Dia
45 Deg
L/4
L/4
L/4
L/4
L = 90 ft. (27.7m)
10
9
Conveyor Belt
Fabric Splice Manual
Conveyor Belt
Fabric Splice Manual