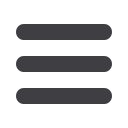
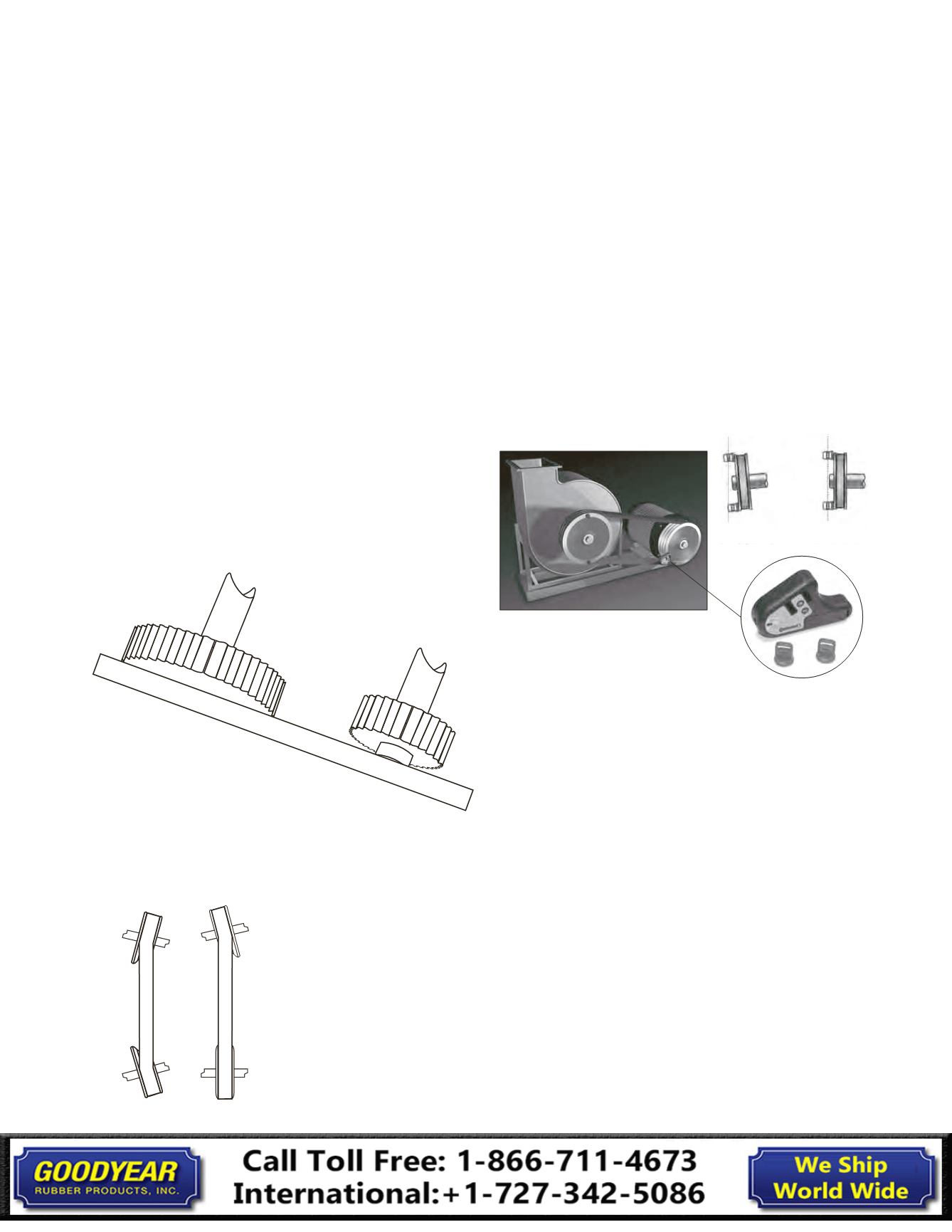
Misaligned
Aligned
9. Check Alignment
Drive Alignment
Synchronous belts are very sensitive to misalignment.
The tension carrying member has a high tensile strength and
resistance to elongation, resulting in a very stable belt product.
Any misalignment will lead to inconsistent belt wear, uneven
load distribution and premature tensile failure. In general,
synchronous drives should not be used where misalignment is
a problem. Limit misalignment to 1/4 degree or approximately
1/16 inch per foot of center distance. With parallel shafts,
misalignment occurs when there is an offset between the
sprocket faces as in Figure A.
Misalignment also occurs when the shafts are not parallel as in
Figure B.
Laser Alignment Tool
With our Laser Alignment Tool, you can quickly align drive
components to improve efficiency and reduce costly
maintenance. Much easier to use than a straight edge, it
attaches in seconds and when the highly-visible sight line lies
within the target openings, the pulley/sprockets are aligned.
10. Identify correct belts
Always select belts to match sprocket profile. SilentSync® belts
and sprockets are identified with a unique Color Spectrum
System. The seven colors used for identification are: Yellow,
White, Purple, Blue, Green, Orange and Red. Each color
represents a different size so that Blue belts are made to
operate with Blue sprockets. Make sure to obtain the same
color belt and sprockets. When installing other synchronous
belts, use the correct sprocket width.
11. Matching belts
Drives using synchronous belts are not recommended to run in
matched sets. If a special application requires matching, specify
“matched belts” on the order. Note: such requests require
additional order lead time. Also, matching code numbers will not
appear on the belts.
Figure A
Figure B
38
Synchronous Belts
Installation Guide