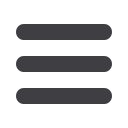
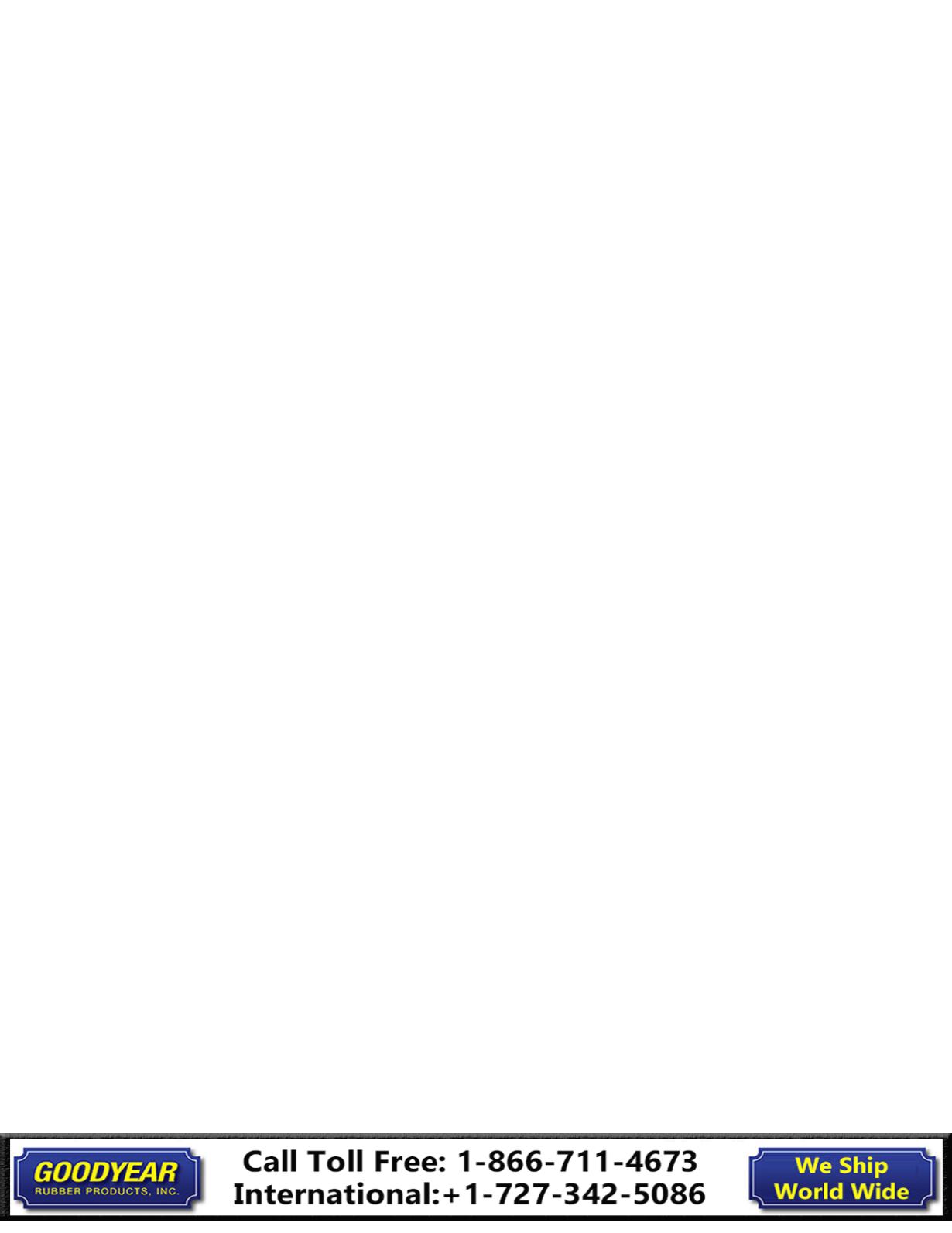
The following few sections detail other
issues that could arise during synchronous
belt installation:
14. Using a fixed center distance
A fixed center distance drive has no adjustment for
tensioning or installing the belt. Due to the tolerances of drive
components, including sprocket, belt and drive geometry,
a drive with a Fixed Center Distance is not recommended
as adequate belt tension cannot be assured. Proper belt
installation requires a minimum center to center adjustment
(refer to belt installation for center to center adjustment on
page 39). In some cases, fixed center drives cannot be avoided
and should be used only with the understanding that belt life
will be reduced.
15. Design factors
To ensure proper belt selection, consult the appropriate
design manual for SilentSync,® Blackhawk Pd,® Falcon Pd®
or Hawk Pd.® Due to the high load capacity of these belts, make
sure that all of the drive components are adequately designed.
Consult sprocket and other component manufacturers for
design assistance or if verification of application is needed.
16. Belt guards
Belt guards ensure cleanliness and safety. Screened, meshed,
or grilled guards are preferable because they allow for air
circulation and heat escape.
17. Idlers
Use idlers either inside or outside of the belt, preferably outside.
Idlers often function as a tensioning mechanism when the drive
has a fixed center distance. When an idler is necessary, follow
several general rules:
Locate the idler on the slack side of the belt.
Small, inside idlers should be grooved (up to 40 teeth).
Outside idlers should be flat, not crowned.
Minimum idler diameter should be 4 inches on 8mm pitch
drives and 8 inches on 14mm pitch drives.
Hold idler arc of contact to a minimum.
Do not use spring loaded tensioners.
42
Lock idlers firmly in place to minimize movement or deflection
during drive start-up and operation.
18. Teeth in mesh
Sprockets with low belt angle of less than 60 degrees or less
than six teeth in mesh (TIM) will not transmit the full rated load.
Should drives be designed using less than six teeth in mesh, the
service life of the belt will be reduced.
19. Flanged sprockets
Use flanges to keep the belt in the sprocket and prevent
“rideoff” as each belt has its own tracking characteristics. Even
belts with perfect drive alignment can have a tracking problem.
Synchronous belts will have an inherent side thrust while in
motion and can be controlled with flanged sprockets. If side
thrust is severe, check the drive for sprocket alignment, parallel
shafts and shaft deflection.
For a two sprocket drive:
A minimum requirement should be two flanges on one
sprocket for economical reasons; the smaller sprocket is
usually flanged.
When the center distance of the drive exceeds eight times the
diameter of the smaller sprocket, it is suggested that flanges be
included on both sides of each sprocket.
On vertical shaft drives, one sprocket should be flanged on
both sides and one sprocket flanged on bottom side only.
For a multiple sprocket drive:
Two flanges are required on every other sprocket or a single
flange on every sprocket, altering sides.
Synchronous Belts
Installation Guide