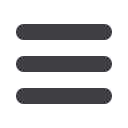

Stringing the Belt
Textile belts that have been slit from a full width slab at the
factory should be spliced with the factory cut edges on the
same side of the conveyor. The words “Fact Edge” are painted
on the factory edge of slit rolls.
If the Factory Edges cannot be matched to the same side for
splicing, one of the slit rolls will need to be re-rolled; such rolls
will be identified with “Re-rolled” painted on the belt’s edge.
For new installations and major replacements, the following
procedure is recommended for belting with Sensor Guard
®
loops
or Cord Guard
™
XD Rip Inserts. Each roll of belting will be clearly
identified with a roll number.
›
The first end cured at the factory will be attached
to the shell.
›
The last end cured in the factory will be the outer wrap.
›
Typically and unless otherwise specified, the top cover will
face “outside”.
All rolls of belting are to be spliced onto the conveyor in the
following sequence starting with the last manufactured roll
(e.g. roll #8 of a total of 8).
›
The inside wrap of roll #8 will be spliced to the outside wrap
of roll #7.
›
The inside wrap of roll #7 will be spliced to the outside wrap
of roll #6 and so on.
After the belt has been positioned, the means of threading it on
the conveyor system must be considered. If the new belt is a
replacement, the old belt can be used to pull it on. A method to
pull belting on the system is as follows: The old belt is clamped
off, cut and the new belt then spliced to the end of the old belt
using plate type fasteners or pulling plates as illustrated
in Fig. 2-4.
The trailing end of the old belt is connected to a suitable power
device to pull the belt through the system. The conveyor drive
motor can be used to pull on the new belt. Other suitable
pulling devices such as cord winches, belt winders and
bulldozers, can also be used. See Fig. 2-5.
For a new conveyor installation having little or no slope, a rope
or cord of suitable strength should be attached to steel pulling
plates. The rope or cord is then threaded around the conveyor
system and attached to a suitable power device to pull the
belt into place.
A belt being installed on a system with a relatively high degree
of slope (12 degrees or more) must be handled with more
precaution to guard against run-away. The belt roll is set up as
previously mentioned, usually at or near the head pulley. This
is generally the most accessible. Assuming the conveyor is
sufficiently long to require more than one splice, the carrying
side and the return side may be threaded on separately. Care
must be taken to see that the heavier cover is up on the
carrying side and down on the return run.
NOTE: If belts are to be strung on both the carrying and return
side of the system, then re-rolling of the belts for one of the sides is
necessary before stringing to ensure the correct sequence in splicing.
For major installations, rolls can be shipped in this configuration
by prearrangement.
As the belt is fed on the system, tension at the roll tends to build
up due to the weight of the belt on the slope. For this reason,
some method of braking is required, such as using a belt clamp
mounted on the conveyor structure, through which the belt
is threaded. Where the slope is very long, additional clamps
should be used, spaced approximately 1000 feet (305m)
apart. Mechanical, air and hydraulic clamps are recommended.
Wooden clamping devices are not recommended.
To estimate the pull required to hold a belt on a slope, multiply
belt weight (lb./ft.) times the vertical lift of the slope and add
10%. For example, assume a 40-lb./ft. belt and a 300-ft. (91m)
high slope. The approximate pull is (40 x 300) x 1.1 = 13,200 lb.
Fig. 2-4: Pull Plate for Fabric Belt
Sharpened Driving Bolt
Eye and Shackle Designed for Load
Cut-off Protruding Ends
Bottom Plate
Belt
Material:
1. 1/2" to 3/4 in. Plate
2. Top plate about 8".
square held back 1".
from leading edges.
Match drill bottom plate.
Fig. 2-5: Typical belt winder (with snub roll) set-up.
II. Belt Installation
Belt Storage and Installation
1.
The methods of storing and handling Conveyor Belting
and the procedures for tensioning it before making
the final splice are just as important as actually making
the splice.
2.
New conveyor belting should be stored upright in the
factory package until used. A cool dry room, free from
sunlight, steam pipes, oil and corrosive fumes is best.
Under no circumstances should a roll of belting be
stored on its side, even if on a concrete floor.
3.
Moisture will shrink any exposed fabric that gets damp
from such storage and the belt may “bow” on one edge.
4.
Storage of rolls in an upright position on a dry floor is
preferred. If long-term outside storage is necessary, the
lay-down area should be prepared by placing matting
or other material to protect the belt from sharp objects.
5.
If long-term storage outside (more than one year)
is necessary, the belt must be covered with a suitable
material such as a tarpaulin or heavy pigmented
plastic sheeting. This will protect the belt from the
effects of weathering.
Handling the Roll of Conveyor Belt
1.
Conveyor belts should never be dropped while unloading
from a freight car, truck or other means of transportation.
Due to their weight, dropping rolls can break the
packaging and may damage the belt.
2.
Belts should never be rolled or skidded. Provisions should
be made to use proper moving equipment. Care must be
taken when hoisting a conveyor belt to prevent damaging
the edges. Insert a bar through the center of the roll and
lift with cords or chains attached to a spreader (Fig. 2-1).
3.
Once the roll of belting has been transported to the
installation area, it should be mounted on a suitable shaft
for unrolling and stringing onto the conveyor system.
4.
Conveyor belting may be rolled at the factory with the
carrying side out or in depending on customer requests.
5.
Typically the carry side is rolled at the outside.
Consequently, in mounting the roll, the belt must lead off
the top of the roll if it is being pulled onto the troughing or
carrying idlers but off the bottom of the roll if it is being
pulled onto the return idlers. However, if the carry side of
the belt is rolled to the inside then the belt will be pulled
off in the opposite manner.
6.
Fig. 2-2 illustrates a suitable method of mounting a belt
with the carrying side out and leading off the top of the
roll when pulling onto the troughing idlers.
7.
To prevent the belt roll from over-running at the let off, a
braking device is recommended (Fig. 2-3).
Fig. 2-2
Note: Temporary flat
roll at bend point, as
roll is pulled onto
troughing idlers.
Fig. 2-3
Let-off System with Brake
Square to Round Shaft
Band Brake Material
Tensioning Means
Let-off Stands
Fig. 2-1: Proper Belt Handling
6
5
Conveyor Belt
Fabric Splice Manual
Conveyor Belt
Fabric Splice Manual