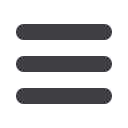

Press Platen Cooling
To prevent blistering, the vulcanizer should be cooled to 130°F
(55°C) or less, before releasing pressure. This is a good practice
at all times since unexpected blisters are undesirable and
require repair or sometimes a complete remake of the splice.
After the splice is cured, remove release material. If Holland
cloth is used, a water soak may be necessary. Trim and/or buff
the overflow at the edges. Do not leave the belt on a
hot vulcanizer.
When Without Platen Cooling
It is not recommended to use a vulcanizer that does not have
cooling capabilities. Leaving a splice in a hot vulcanizer while
it cools without the aid of flushing water or air will result in
over-curing the splice rubber. Overcooked splice rubber is a
leading cause of premature splice failures. Overcooked splice
rubber will not perform as well as splice rubber that has
achieved Ultimate Cure.
1.
This section is included only to address those rare
instances where the vulcanizer is not fitted for water
cooling ports.
2.
At the completion of the specified cure time, TURN OFF
THE HEATING ELEMENTS, RELEASE THE PRESSURE AND
REMOVE THE TOP PLATEN IMMEDIATELY. This procedure
is necessary to avoid over curing the splice.
3.
DO NOT ALLOW THE BELT TO REST ON THE HOT
BOTTOM PLATEN. Either remove the bottom of the press
or carefully elevate the belt to provide an air space for
cooling. Lift the belt from the press using a support bar at
each end of the splice.
4.
Proceed on to Splice Completion.
Splice Completion
After the cure cycle is finished and cooling the press has
been completed:
1.
Remove the top platen of the vulcanizer.
2.
Remove edge guides and fill steel.
3.
Remove top thermocouple wires.
4.
Remove release paper.
5.
Inspect the splice for any abnormality such as blisters, ply
blows, gum blows, porosity etc.
6.
Repair and document any abnormality seen.
7.
Buff the overflow at the fill strip area. Buff in the direction
from the fill strip into the belt. Buff and remove the rubber
overflow until a flat, smooth transition from the belt to the
splice is achieved.
8.
Perform the same inspection and buffing on the bottom fill
strip area.
9.
Remove all vulcanizing tools, equipment and materials.
Properly dispose of all trash and leftover splice materials.
General Curing Notes
1.
The area between the steel guides and the outside
edge of the vulcanizer should be filled to avoid possible
platen distortion or damage. Steel or aluminum guides
may be evenly spaced approximately 6 in. to 10 in.
(152mm - 254mm) apart.
2.
To help release steam on an obviously wet belt, an
awl should be used to perforate the belt every 2 in. - 4 in.
(50mm - 100mm) along the vulcanizer ends.
3.
Though not recommended there are instances when the
vulcanizer dimensions are such that a splice will be cured
in two or more heats.
In these cases:
›
Begin at one end of the splice.
›
The cover (fill-in) strips should be completely cured in a
single heat.
4.
The bias length is sometimes adjusted (a few inches) so
the full splice length can fit in the vulcanizer and be cured
in one cook cycle.
5.
The bottom platen must be 6 in. to 8 in. (152mm to 203mm)
wider and longer than the splice. Center the splice on the
bottom platen making certain there is approximately
3 in. to 4 in. (75mm to 100mm) of platen extending past
its edges and ends.
Power Failure: 50% Rule
In case of a power failure while curing, do not release the
pressure, but hold it until power is restored and then bring the
vulcanizer back up to cure temperature. At that time:
1.
If the splice had less than half of its specified cure time
before power failure, repeat the entire specified cure
time. If the splice had cured half or more of the specified
time, then finish curing the remaining time after all
thermocouples again register the specified temperature.
2.
Someone must be monitoring and documenting the cure
cycle of the splice. This person must know and be able to
react if necessary to perform the 50% rule procedure.
Pressure Failure
If vulcanizing pressure is lost on the surface of the splice,
it must be remade. It is not recommended to use the
same sections of the belt ends to re-splice. It is strongly
recommended to remove the sections of the splice that
experienced loss of pressure.
Vulcanizing the Splice
Careful preparation has been completed to build the
splice according to the manufacturer’s specifications and
recommendations. The same detail must be applied to curing
the splice.
The goal is to achieve ultimate cure of the splice rubber. The
vulcanization of rubber compounds needs to be carefully
controlled and monitored to ensure optimum rubber
properties for maximum splice life. Ultimate Rubber Cure
is a result of controlled time and temperature. Curing at a
higher than specified temperature or altering the cure time
may jeopardize the possibility of achieving Ultimate Rubber
Cure. Within the splice it is critical to allow the rubber to work/
perform as it is designed.
Vulcanization, as a rule of thumb, doubles in the rate of cure
for every 18°F (–7.7°C) change in temperature. Over-curing,
a splice can be as detrimental as under-curing. Temperature
controllers and measuring devices on vulcanizing equipment
should not be relied upon to provide a dependable
assessment of the actual platen temperatures. For this reason,
each individual heating element in a platen must be monitored
with a thermocouple placed on the surface of the belt. A
properly calibrated thermocouple unit connected to a chart
recorder or other suitable data acquisition unit is required.
During a cure, it is the responsibility of a member of the splice
crew to observe the temperatures of each thermocouple
and continually adjust the press control units to maintain
temperatures within 0° to 5°F (–17.7 to –15°C).
It is recommended that all field vulcanizers temperature
controls and measuring equipment be regularly maintained
and calibrated to minimize the amount of manual adjustment
required during a cure cycle.
1.
Cure times and temperatures are shown on Table 4-1.
2.
The timing of a splice cure is not to start until
all thermocouple readings have reached the
specified temperature.
3.
It is recommended to use a splice shelter or tarpaulin over
the vulcanizer/splice area to keep the splice dry, minimize
heat loss, and promote uniform heating in windy and cool
conditions.
4.
Due to heat radiation, the splice and belt ends must
be centered on the bottom platen. The splice and belt
ends must be 3 in. - 4 in. (75mm - 100mm) inside the
platen edges.
5.
The splice must not be put into service until it has cooled
to 130°F (54.4°C) or lower.
Belt Thickness (mm)
Inches
Fabric Belt
Cure Time (min)
up to 3.1
up to 1/8
20
3.1 - 6.3
1/8 - 1/4
25
6.3 - 9.5
1/4 - 3/8
25
9.5 - 12.7
3/8 - 1/2
30
12.7 - 15.8
1/2 - 5/8
35
15.8 - 19.0
5/8 - 3/4
35
19.0 - 22.2
3/4 - 7/8
40
22.2 - 25.4
7/8 - 1
45
Add 5 min. for Neoprene Belts over 1" Gauge (25.4mm)
25.4 - 28.5
1 - 1
a
50
28.5 - 31.7
1
a
- 1
e
50
31.7 - 34.9
1
e
- 1
b
55
34.9 - 38.1
1
b
- 1
f
60
38.1 - 41.2
1
f
- 1
c
60
41.2 - 44.4
1
c
- 1
g
65
Table 4-1: Fabric Belt Cure Pressure is 100 psi - 130 psi (.69 - .89 MPa).
18
17
Conveyor Belt
Fabric Splice Manual
Conveyor Belt
Fabric Splice Manual