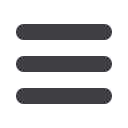

Porcupine Roller and Stitch Rollers
The porcupine roller and stitch rollers are used to roll rubber
sheet flat and remove possible trapped air.
Identification
1.
Tools identified below are typical splicing hand tools.
Always use the proper tool for the job.
2.
Use the proper PPE and handling/application
safety procedures
Miscellaneous Items
1.
A winch/tugger will greatly reduce the time spent stripping
the belt ends.
2.
Power is a prerequisite when tearing down fabric reinforced
belt ends. An air or electric winch is typically used.
3.
Water, for cooling the vulcanizer.
4.
Appropriate power supply to operate electric buffers,
tuggers, etc.
5.
Thermocouple unit and pressure transducer with
chart recorder.
6.
Required personal safety equipment.
Fig. 3.4: Fabric Belt Splicing Tools.
1. Rubber and fabric pulling device
2. Thermocouple unit and wires
3. Buffer
4. Sharpening Stone
5. Square
6. Awl
7. Ply lifting clamp
8. Tape
9. Foxtail brush
10. Stanley knife
11. One-ply knife
12. Pricker roll
13. Flexible skiving knife
14. Ply prodder
15. Small square
16. Scissors
17. Silver pen
18. 4" roller
19. Folding ruler
20. Dull and rounded knife
21. 1/16 in. stitcher
The Work Table
1.
Laying out the splice and cutting of the plies must be
done on a flat, smooth surface. The bottom platen of the
vulcanizer is used as the center section of the work area.
2.
The work area surface should be 6 in. (150mm) wider than the
belt being spliced and at least 4 ft. (1.2m) longer than the splice.
The surface should be one piece or smoothly joined and firmly
held in position. Plywood with a thickness of 5/8 in. – 3/4 in.
(15mm – 19mm) is usually sufficient.
3.
The table must be elevated to provide clearance for
clamps used to hold the belt ends in alignment.
Splice Tools
It is strongly recommended to use the correct splicing tool
needed to perform specific tasks. One very important tool is
the Fabric Ply Knives. The Fabric Ply Knives are designed to
cut at a given depth and prevent cutting or damaging the
adjacent plies.
Fabric Ply Knives
1.
Typically there are two types of ply knives used to accurately cut
plies without damaging/nicking the adjacent ply.
›
The 0.040 ply knife is generally used for the lighter
weight fabrics up to and including 150#.
›
The 0.080 is generally used for heavier weight fabrics such
as 200# & 250#. For fabrics such as 400# - 450# and greater,
hook knives are typically used.
2.
Do not attempt to sharpen these knives. Sharpening them
will increase the hook depth and may result in damaging
the adjacent ply.
3.
The “One-Ply” knife, as the name implies, is intended to cut
only one ply. Therefore, certain points should be carefully
observed.
4.
The depth of the cutting edge should be sharp and
ap
proximately 75% of the thickness of one ply of the fabric
being cut. Various weights and types of fabric require
different depths of the cutting edge (Fig. 3-1).
Fig. 3-1: One-Ply Knife.
5.
The knife should be held at approximately 45° from the
belt surface so that the land of the knife will be flat on the
ply below the one being cut.
6.
Practice sessions using the ply knives are recommended.
CAUTION : A high percentage of fabric splice failures are caused by the
one-ply knife nicking, cutting or gouging the adjacent ply.
Inspect one-ply knives frequently and see that the hook or cutting edge
is not too deep. Regardless of the condition of the knife, it is possible to
cut through more than one ply and the operator should always watch
this closely. Keeping the knives in proper condition is important.
Never cut deeper than intended, or cut into or destroy any fabric,
which is to remain a part of the splice.
Mill Knives with Dull Rounded Tips and Sharp Cutting Edge
These knives are used to cut through the cover rubber without
damaging/nicking the adjacent ply.
Adjustable Olfa Knives or Box Knives
1.
These knives typically have razor-sharp tips and edges and
can cut into adjacent plies very easily.
2.
These knives should not be used or take the place of the
ply knives to step down fabric splices.
Prodders
:
1.
Prodders are used to separate the inside rubber from
the stationary fabric ply. The prodding tool must be dull,
rounded and smooth. Burrs and/or nicks on the tip will
cause damage to the fabric ply. The care and handling of
the ply lifter/prodder is important.
2.
The corners should be rounded.
Approx. 1/8 in. (3mm) radius is
recommended. Sharp corners will
injure the ply beneath the one being
loosened (Fig. 3-2).
3.
After considerable use, the edge at
the end or tip of the prodder
(Fig. 3-2) will become worn and
sharp. This should be kept dull,
rounded and free from burrs.
4.
Use the ply lifter/prodder so that it is parallel to the cut
and held at an approximate 30° angle from the belt. The
flat end or tip of the ply lifter should also be at about a
30° angle from the belt. In this manner, it will loosen the
edge of the fabric without “digging into” or injuring the
next ply (Fig. 3-3).
Fig. 3-2: Ply Lifter
1/8 in. Radius
End or Tip
Fig. 3-3:
Improper care
and use of the
ply lifter may
also damage
the adjacent
ply and may
contribute to
splice failure.
12
11
Conveyor Belt
Fabric Splice Manual
Conveyor Belt
Fabric Splice Manual