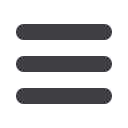

Pulley
Cover
Top
Cover
TCG
Skive Line
Middle
Ply
Bottom
Ply
Skive Line
PCG
13.5 ft.
Sec View
C-C
Width
Part A
Top Cover
Facing “UP”
Top
Ply
7.50 in.
7.50 in.
6 in.
6 in.
6 in.
30 in.
30 in.
22°
Bias
C
NOTE: Bias to Match Vulcanizer
C
Bias Step Finger Splice
1.
The Bias Step Finger Splice is made as a Bias Step Splice
with finger cut out at the end of each ply.
2.
The fingers are necessary to allow better flexibility in the
splice as it travels around pulleys while under very
high tensions.
3.
Currently, only a few Bias Step Finger Splices are specified.
The list of Bias Step Finger Splices may include but not be
limited to the following:
›
1350 PIW x 3 ply
›
1500 PIW x 3 ply
›
1800 PIW x 4 ply
›
2000 PIW x 5 Ply
›
2500 PIW x 6 Ply
NOTE: Each of the following belt types may also be spliced using the
Long Life Full Carcass Finger Splice. However, it is not recommended or
specified to use the Bias Splice Step Method to splice them. A minimum
cover gauge of 3/32” is required for a long life full carcass finger splice
(1/8” minimum is preferred).
4.
These are general instructions for performing a vulcanized
Bias Step Finger Splice only. For further reference for this or
any other type of authorized Continental ContiTech splice,
contact your local Sales Representative.
NOTE: The references to the TOP and BOTTOM are relative to the belt
on the working surface, NOT the actual top and bottom of the belt. I.e.
when splicing with the pulley cover UP, the top cover (as referenced
here) will be the pulley cover.
5.
Refer to the specified splice schematic for detailed splice
dimensions before starting the splice.
6.
The Bias Step Finger Splices are drawn out in the same
manner as straight Bias Step Splice except you will add
fingers at the end of each ply.
7.
Strip down the belt ends as a Bias Step Splice then cut out
the fingers. Refer to Fig. 6-1.
8.
The fingers are cut at the end of each ply. Fingers are
typically 6 in. (150mm) long x 4 in. (100mm) wide.
9.
Check the system for the direction of travel. This will be
important during the finger layout. Layout splices so that
the pulley cover insert leads the splice into the drive.
10. Align one end on the bottom platen; identify bias to match
your machine.
35. To ensure solid edges, guides of the proper gauge must be
used. The guides must contact the belt edges for the full
length of the splice and extend 6” (150mm) beyond both
ends of the press (Fig. 5-20).
NOTE: An exception to the above splice directions sometimes occurs
when splicing a new belt into an old one. If the old belt covers are
badly worn then both ends of the new section should be stepped from
the pulley side. This leaves new unworn top cover on both splices and
will provide more uniform vulcanizer pressure. In doing this, one splice
will run in reverse to the usual recommendation.
36. After cure, trim the edges of the splice. It is normal for the
fabric joints to be spaced 1/4 in. (6mm) or so during cure
due to shrinkage.
37.
Refer to Section 4 vulcanizing of this manual for
vulcanizing instructions.
38. The splice must not be put into service until the splice
has cooled at least 130°F (54°C) or to the ambient
temperature.
39. Buff inserts and overflows down to original belt gauge to
prevent damage from scrapers.
40. Complete all necessary documentation for the splice,
splicing procedure, splice materials and splice cure.
Fig. 6-1
Fig. 5-20
26
25
Conveyor Belt
Fabric Splice Manual
Conveyor Belt
Fabric Splice Manual