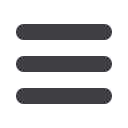

1.375"
0.156"
Table 9-1
Example:
1000/4 1/4X3/32 U38 - OAG= 0.710 - Does not require pulley cover skive
1000/4 1/4X1/4 U38 - OAG= 0.868 - Must skive pulley cover
.156 in. +/- 0.020
.1.375 in. +0.063 -0.000
Fastener Application Cover Skive Instruction
For heavyweight belting with covers
≥
1/4 in. (6mm) top cover
and MATO fasteners
1.
For MATO fasteners set top cover skive reach back to
1⅜ in. (35mm). (Fig. 9-8)
Fig. 9-8
2.
For MATO fasteners set top cover skive depth to remove
5/32 in. (4mm) of the top cover. (Fig. 9-9)
Fig. 9-9
3.
Please see Table 9-1 for additional pulley cover
skive requirements:
4.
Verify the skive dimensions below (Fig. 9-10):
Fig. 9-10
5.
Buff top corner of cover skive across the width of the belt
“smoothing out” the rectangular point of the skive (Fig. 9-11)
Fig. 9-11
Fig. 9-4
Fig. 9-5
Fig. 9-6
Cable pin
Pointed rivet
2. Hinged Plate Fasteners
A variation of the plate fastener uses the same bolt and plate
attachment to the belt ends but has a hinged connection
between the two ends with a removable pin. This permits
taking the splice apart more readily, at the expense of some
leakage of fine material and slightly less strength. This class of
fastener is extensively used underground where conveyors are
frequently extended or retracted. Fig. 9-4 illustrates a fastener
of this type.
3. Riveted Plate Fasteners
A further variation of the hinged plate-type fastener uses rivets
to hold the fastener to the belt ends. Fig. 9-5 and Fig. 9-6 give
some examples of these types.
4. Hook Type Fasteners
Hook Type fasteners attach to the belt ends by means of hooks
formed from wire or sheet steel. They are applied by forcing
the hooks through the belt and clinching on the opposite side.
All these types have a hinge pin or rocker pin joint and can
be taken apart easily. They permit somewhat more leakage
of fine material. The clinching technique of these fasteners
has improved in recent years allowing application of this class
fastener for higher tension belts. These types are particularly
suited for package conveying where their relative smoothness
is an advantage as in the case where packages are plowed off
the belt. Fig. 9-7 illustrates this type.
Fig. 9-7
Tightening Fasteners
Extensive testing has proven the necessity for retightening
fasteners on a periodic schedule, usually after a few hours of
operation, after a few days of operation and then, at intervals
of two or three months. This does not preclude, however,
retightening at intervals that are more frequent if inspection
indicates this to be necessary.
Hazard to the Belt
Failure to inspect fasteners and resulting failures may be
a cause of severe belt damage. Particularly, pulling out of
fasteners for a portion of the belt width can start longitudinal
ripping of the belt. When belt and fasteners have been properly
selected, pullout is usually due to insufficiently tight bolts or to
worn hooks or plates.
Fasteners for Special Requirements
Many fasteners are available in a variety of different metals
designed for special applications. These applications include
nonsparking, nonmagnetic, abrasion resistance and chemical
resistance. The manufacturer should be contacted for the proper
recommendation to be used with any specific application.
38
37
Conveyor Belt
Fabric Splice Manual
Overall Belt Gauge
Fastener Type
0 - 0.550 in. (d.)
0.550 - 0.750 in. (d.)
0.750 - 0.875 in. (d.)
0.875 - 2.000 in. (d.)
U35
No Pulley Cover Skive
Skive Pulley Cover using
standard procedures
Skive Pulley Cover using
standard procedures
Skive Pulley Cover using
standard procedures
U37
No Pulley Cover Skive
No Pulley Cover Skive
Skive Pulley Cover using
standard procedures
Skive Pulley Cover using
standard procedures
U38
No Pulley Cover Skive
No Pulley Cover Skive
No Pulley Cover Skive
Skive Pulley Cover using
standard procedures
Conveyor Belt
Fabric Splice Manual