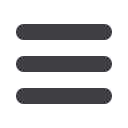

Mechanical Splice
General
In those cases where belt ends are joined with mechanical
fasteners, the first requirement for a good splice is that the belt
ends be cut square. Failure to do so will cause some portion
of the belt adjacent to the splice to run to one side at all points
along the conveyor. New belts can usually be squared with
sufficient accuracy by using a carpenter’s square and working
from the belt edge. Used belts may have an indistinct edge, due
to wear, and should be square from a center line established
by measuring from the edges at a number of points extending
back 15 ft. to 20 ft. (5m to 7m) along the belt. This latter
method will provide even greater accuracy on new belts.
Major classes of mechanical fasteners include: 1) Bolted Plate,
2) Hinge Plate, 3) Riveted Plate and 4) Hook Type. Since the
optimum performance depends on belt construction, service
conditions, pulley diameters and tension, it is recommended that
the fastener manufacturer be contacted for proper selection.
You may select the recommended Fastener Plate Type
to match the specified belt type from the Heavyweight
Conveyor Belt Catalog.
Squaring the Belt End
Swinging Arch Method (Fig. 9-1)
›
Carefully mark a point at the center of the belt width. From
this center point, measure equal distances along both edges
of the belt towards the belt end and mark each edge. These
two diagonal measurements must be equal coming from the
center of the belt’s width.
›
Draw a straight line connecting these two points or use a
straight edge and cut the belt end.
Square to validate the
square line is straight
Square belt end line
1
2
3
4
5
6
7
8
12345678910111213141516171819202122232425262728
Fig. 9-2
Square and Straight Edge Method (Fig. 9-2)
›
Near the end of the belt – Use a square and straight edge to
establish a straight line to be used as the square belt end.
›
Check the square line by laying a square along the opposite
edge of the belt.
Classes of Mechanical Fasteners
1. Bolted Plates
A commonly used class for heavy belts handling bulk materials
is the Bolted Plate type. This fastener uses a series of plates
across the belt, on both top and bottom surfaces, spanning
the joint and compressed against and into the belt surface by
a countersunk bolt in each end of each plate and is illustrated
in Fig. 9-3. This class of fastener makes a strong, durable
splice with no gap to leak materials. It is not easily taken apart
however, due to wear and battering of the bolts in service.
Therefore, in some applications requiring frequent opening of
the belt splice, it is not very desirable.
Fig. 9-3
10. The Long Life Full Carcass Finger Splice method requires a
minimum cover rubber gauge of 0.094 in. to 0.125 in.
(2.4mm to 3.2mm) with the 0.125 in. (3.2mm) preferred.
11.
Regardless of which splicing method is used, Continental
ContiTech’s splicing procedures and specification must
be followed.
12. It is strongly recommended to follow the specified splice
schematic. Splice schematics detailing both splice methods are
available and will point out specific splice details/requirements.
13. The splice schematics include:
›
Accurate drawing of the splice
›
Splice dimensions
›
Bias dimensions
›
Cure specifications
Pipe belt conveyor materials.
Pipe belt conveyor materials.
36
35
Conveyor Belt
Fabric Splice Manual
Distance “A”
Equal to “B”
Center mark at center of the belt width
Distance “B”
Equal to “A”
Squared belt end. Cut along this line.
Fig. 9-1
Conveyor Belt
Fabric Splice Manual