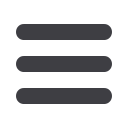
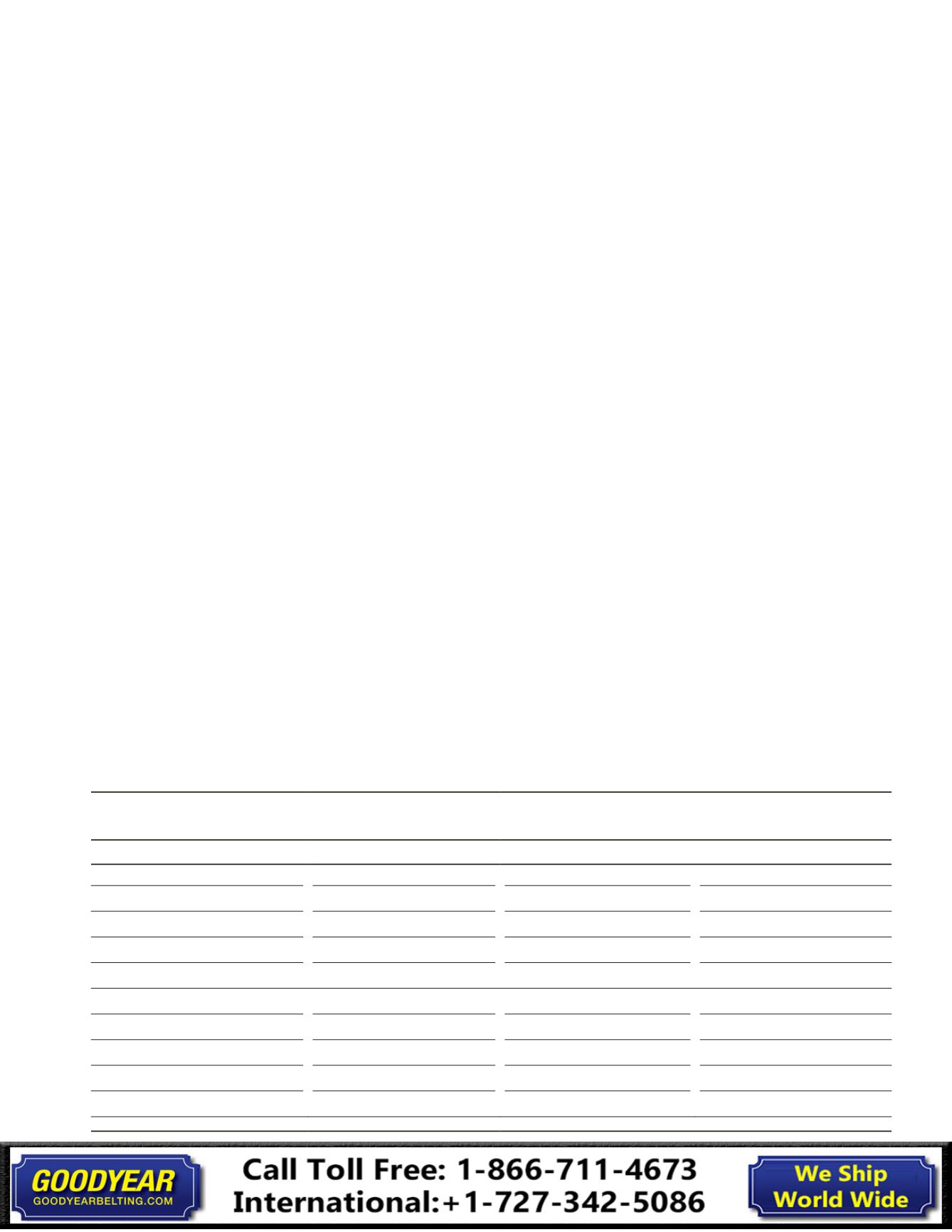
Certain basic statements and recommendations can be made about tensioning
for splicing:
›
Check the belt frequently during tensioning to ensure that
the belt is free and not binding at any place.
›
During the final tensioning pull, be sure the ends of the belt
are lined up properly.
›
Belts which are tensioned by pulling in only one direction
require more splicing tension than those pulled in both
directions.
›
Slope belts spliced at the top of the slope require more
splicing tension than those spliced at the bottom.
›
Slope belts with an anti-rollback device that cannot be
released must be tensioned by pulling only in the direction
of belt travel.
Conveyor installations having limited
take-up travel should be spliced to a
tension based on the loaded running
tension. This tension should be specified
by our engineers and measured by
suitable load cells or dynamometers.
Where it is practical, fabric belts should
be run for several weeks with mechanical
fasteners before making the final
vulcanized splice.
Obtaining the required tension depends
heavily on the experience of the
individual making the splice. It is possible
for a gravity type take-up to severely
damage the conveyor structure if it is
positioned too close to the forward or
upward stop. Too much tension applied
to a relatively short belt may thus have
a harmful effect on the pulley shafts and
bearings as well as the belt.
The belt may be tensioned with a
suitable take-up device as follows:
When the counterweight is on: Tie the
take-up off 6” to 8” (150mm to 200mm)
above the desired running position
(consideration may have to be made for
excessive sag). Next, pull the belt until
the take-up starts to lift and the tie-off
ropes become slack. Make the final
splice, allowing a minimum of belt slack.
When the counterweight is not on:
Splicing without the counterweight
installed is undesirable; however, the
following procedure should be employed
if necessary: Use suitable belt clamps to
hold the take-up pulley 6” to 8” (150mm
to 200mm) above the desired running
position (consideration may have to be
made for excessive sag). Pull the belt to
its running tension, which can only be
estimated in this situation. Judgment in
estimating this tension will improve with
the experience of the splicer.
Tables 1-1 and 1-2 show the recommended take-up travel and initial take-up
position respectively.
6
Installation, Maintenance & Troubleshooting Guide
Installation
Table 1-1 Recommended Minimum Take-Up Travel
In Percent of Center Distance*
Type of take-up and
carcass material [WARP]
Percent of rated tension
Manual take-up**
100%
75%
50% or less
Nylon
4%
3%
2%
Polyester
2.5%
2%
1.5%
Aramid
2%
1.5%
1%
Fiberglass
1%
0.75%
0.5%
Automatic take-up**
Nylon
3%
2.5%
1.5%
Polyester
1.7%
1.25%
0.75%
Aramid
1.5%
1%
0.75%
Fiberglass
0.5%
0.4%
0.25%
Steel
0.3%
1.23%
0.15%
*For [1] belts installed at average empty running tension [2] take-up position per Table 1-2, and [3] Drive location at or near the high tension end of the conveyor.
**Only short endless feeder belts and the like would normally be vulcanized on conveyors with a manual take-up.