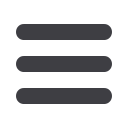
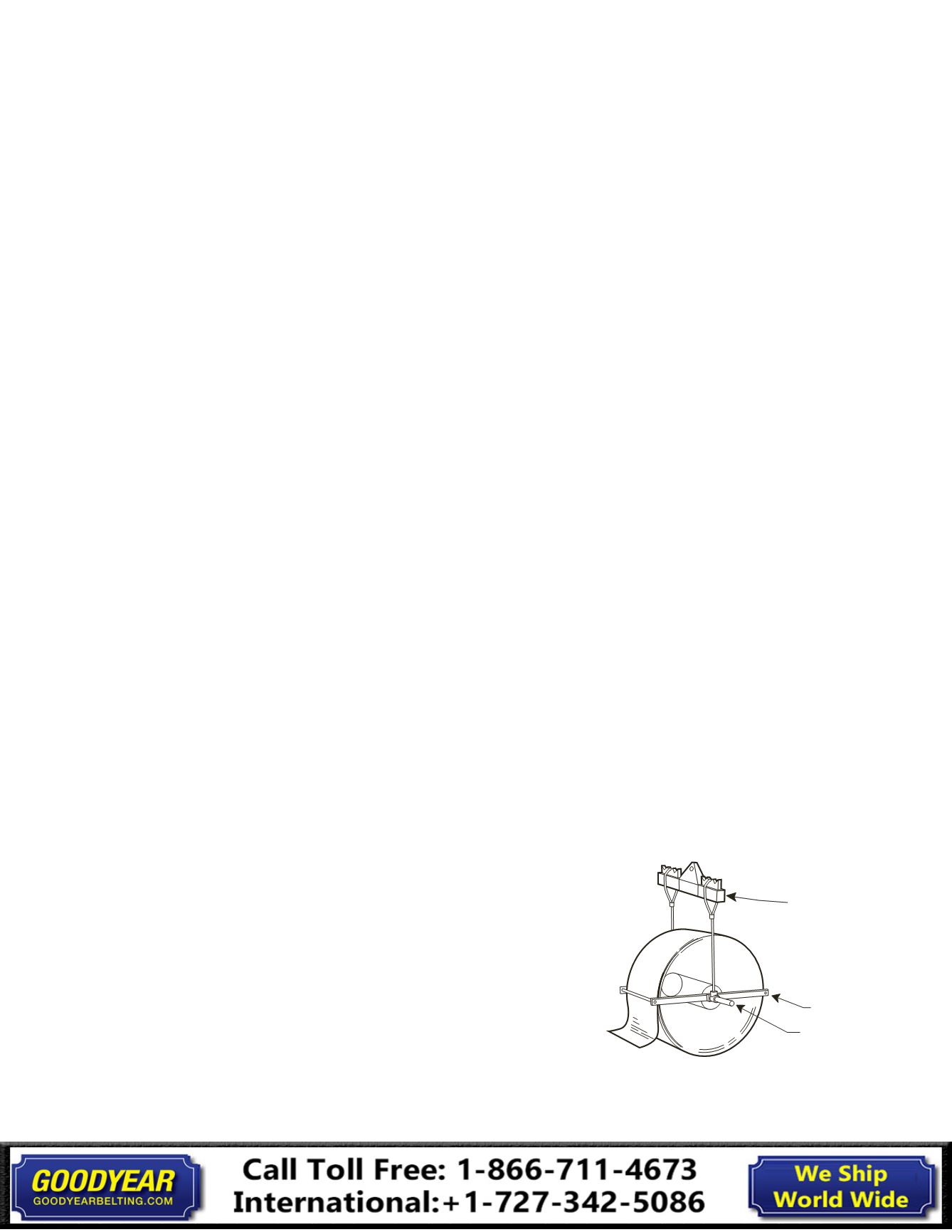
Fig. 1
Center Bar
Keeper
Channels
Spreader Bar
Storage
The methods of storing and handling conveyor belting and the procedures for tensioning
it before making the final splice are just as important as actually making the splice. Protect
your conveyor belt investment with proper storage.
Belts should always be stored upright in the factory package
until used in a cool, dry building and in an area free from
sunlight. If possible, store the belt roll suspended on a tube,
bar or support stand. Where suspension is not possible, the
roll should be stored on a dry surface and rotated 90° every 6
months. Rotation should be performed in the same direction
used to wind up the belt. Rotating in the opposite direction
could cause the roll to loosen or telescope. It is particularly
advisable to rotate a large roll of belting (over 25 tons) to
prevent "flat spotting" (cold flow). This flow under pressure
creates a thinner belt. Although this condition may correct
itself after several months of operation, it is advisable to take
steps for its prevention. If the belt is supplied on a steel reel,
the belt would be considered as "suspended," and therefore
not need rotation. Under no conditions should a roll of belt,
especially raw edge or used, be laid flat on its side. Storing the
belt flat on the ground, where moisture can penetrate exposed
fabric, or storing the belt roll with weight on one edge may
stretch the belt. This can cause belt camber or a bowing in the
belt, resulting in serious belt mistracking.
Handling The Roll
During extended storage, the belt roll should be covered with
a tarp or dark plastic. Exposure to sunlight, rain and ozone
can have detrimental effects on the rubber covers. The cover
should remain in place for the entire storage time.
It is important to make sure the belt is not exposed to extreme
temperatures during storage. Ideal temperature for storing
a belt is between 40°F (4°C) and 90°F (32°C). Temperatures
outside of this range for an extended period of time can have
detrimental effects on the rubber compounds.
As the length of time stored increases, and as the size of the roll
of belting increases, so does the importance of the following
correct storage procedures. Following these procedures will
increase the life of the belt once it is installed on the system.
Even if the precautions outlined in this section are followed,
it is still possible that the outside wrap of each roll may suffer
excessive hardening or cracking during long-term storage. If
this situation occurs, remove the outer turn of the roll to assure
that optimum cover/carcass quality material is used for splicing.
Conveyor belting is customarily packaged
in cylindrical reels, or rolls on a core with
the carrying cover side facing out. If
rolling is necessary, it should occur in a
direction such that the end of the roll on
the outside wrap travels in the direction
from which it is wound up. Rolling in the
opposite direction tends to loosen and
telescope the belt.
Reels or rolls should never be dropped
from a freight car, truck or other means of
conveyance, since their weight will break
the packaging and may damage the belt.
Reels or rolls should always be rolled or
provision should be made for hoisting
them. For hoisting, a square lifting bar of
the correct size should be placed through
the hole in the center of the core. A
spreader bar should be utilized to prevent
the chains or slings from damaging the
edges of the conveyor belt.
Slings or
chains of the correct size for the weight
of the roll should be used (Fig. 1).
1
Installation, Maintenance & Troubleshooting Guide
Installation