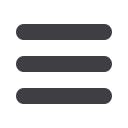
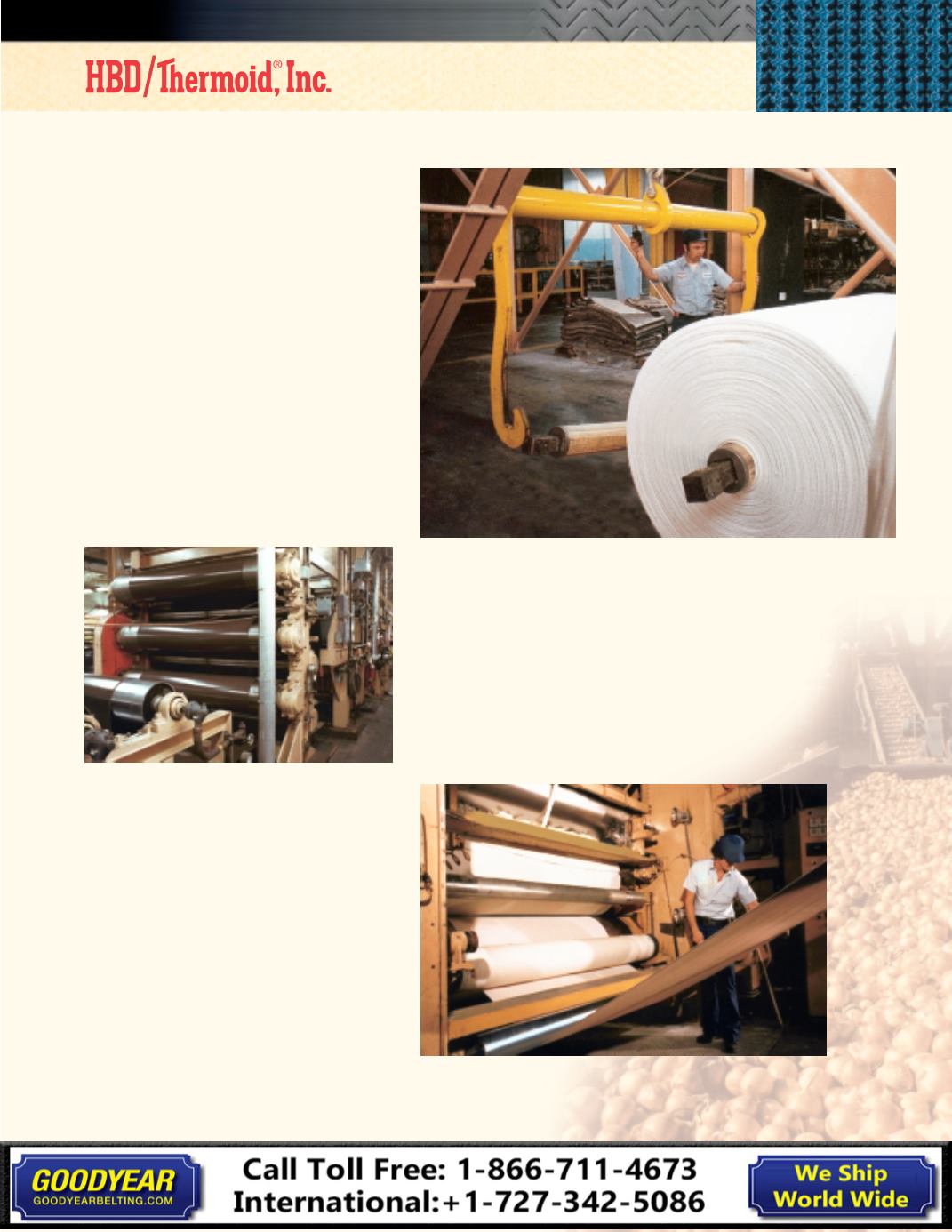
HBD/Thermoid
®
, Inc. has been a leading
innovator in lightweight belt technology
for decades. Many improvements that
have now become industry standards
were pioneered in our research
laboratories.
We were the first to use 100% polyester and
50-50 polyester-cotton blends for greater
strength and moisture resistance in our light-
weight fabrics...the first to use a nitrile rubber
to dramatically improve the oil resistance in
our food belts. We developed the special
adhesive treatment for synthetic carcasses
that helps keep plies from separating.
When it comes to conveyor belt technology,
HBD/Thermoid never lets down, which is
why so many customers look up to us for
engineering excellence.
SPECIALLY DESIGNED FABRICS AND
COVERS FOR CONVEYOR SERVICE
We don’t have to rely on commercial fabrics.
Instead, our textile engineers develop special
weaves designed to handle a wide range of
tensions, loads, pulley sizes and troughing
angles. Our cover compounds are developed
by our own experienced research chemists
to cope with conditions like oil and grease,
heat and cold, chemicals, acids, moisture
and abrasion. So every Made-In-USA
Thermoid belting is designed to give you
maximum service for your dollar.
... THE LEADING EDGE
IN LIGHTWEIGHT BELT TECHNOLOGY
UP-TO-DATE MANUFACTURING CONDITIONS
The HBD/Thermoid plant in Oneida,
Tennessee, has more than 300,000 square
feet, and is a modern belt-making plant using
state of the art equipment. We manufacture
a full-line of lightweight rubber and PVC
conveyor belting under the cleanest
conditions. We’ve invested heavily in this
lightweight belting plant because we intend to
make our belts the very best available.
3
For Assistance:
800/367-0420
or
info@hbdthermoid.com