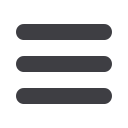
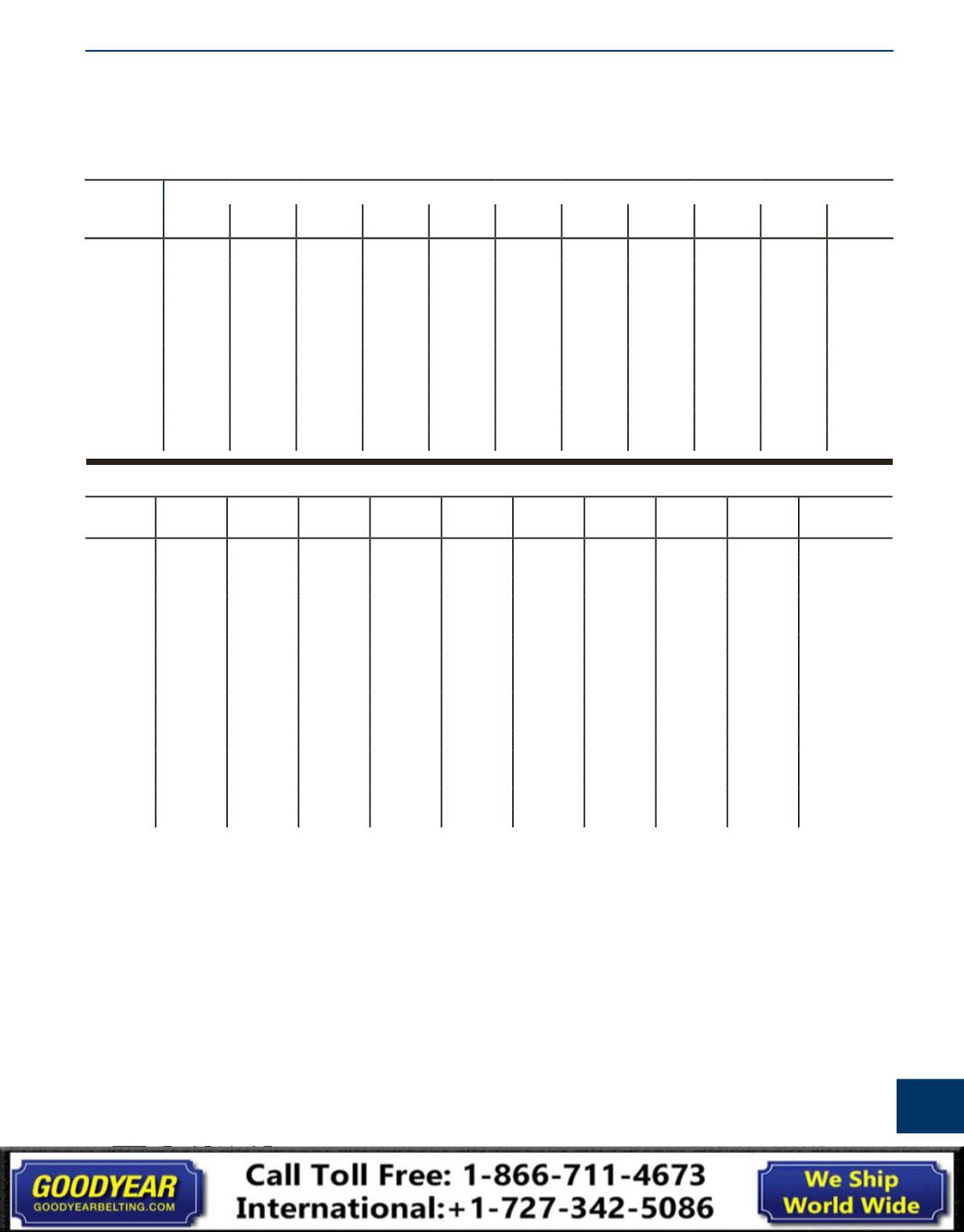
Safety &
Technical
P
935
DPL418
877.963.4966 •
dixonvalve.comP
Applied
Pressure
PSI
Nominal Standard Pipe Size
⅛"
¼"
⅜"
½"
¾"
1"
1¼"
1½"
2"
2½"
3"
5
0.5
1.2
2.7
4.9
6.6
13
27
40
80
135
240
10
0.8
1.7
3.9
7.7
11.0
21
44
64
125
200
370
20
1.3
3.0
6.6 13.0 18.5
35
75
110
215
350
600
40
2.5
5.5 12.0 23.0 34.0
62
135
200
385
640 1100
60
3.5
8.0 18.0 34.0 50.0
93
195
290
560
900 1600
80
4.7 10.5 23.0 44.0 65.0
120
255
380
720 1200 2100
100
5.8 13.0 29.0 54.0 80.0
150
315
470
900 1450 2600
150
8.6 20.0 41.0 80.0 115.0
220
460
680 1350 2200 3900
200
11.5 26.0 58.0 108.0 155.0
290
620
910 1750 2800 5000
250
14.5 33.0 73.0 135.0 200.0
370
770 1150 2200 3500 6100
Maximum Recommended Air Flow (SCFM)
Through ANSI Standard Weight Schedule 40 Metal Pipe
•
Flow values in the table below are based on a pressure drop of 10% of the applied pressure per 100 feet of pipe for ⅛", ¼",
⅜", and ½" pipe sizes; and a pressure drop of 5% of the applied pressure per 100 feet of pipe for ¾", 1", 1¼", 2", 2½", 3" pipe
sizes. The table gives recommended flows for pipe sizes at listed pressures and should be used to determine appropriate
piping for air systems.
Suggested Pipe Size for Compressed Air Flow at 100 PSI Length of Run, Feet
On a compressed air distribution system, pressure losses greater than 3% are considered excessive, and a well-designed
system having a steady rate of air flow is usually designed for not more than a 1% loss or 1 PSI for a 100 PSI system. The pipe
size depends not only on the volume of air flow but how far it must be carried. To hold the distribution loss to 1 PSI, pipes of
larger diameter must be used on longer runs to carry the same flow that can be handled by smaller pipes on shorter runs.
Figures in the body of the chart above are pipe sizes recommended on a 100 PSI system to carry air with less than 1 PSI loss.
When measuring lengths of runs, add 5' of length for each pipe fitting. If carrying 120 PSI pressure these sizes will carry slightly
more air than shown, or pressure loss will be slightly less than 1 PSI. If carrying 80 PSI pressure these pipes will carry slightly
less air at 1 PSI pressure loss than shown in the chart.
The left column of the chart shows the volume of air to be carried. It is difficult to estimate the air flow volume to be carried in
each leg of the distribution system. This varies with the application. On some applications, like in a large plant with many legs in
the distribution system serving dozens of air-operated machines, the air usage may be at a fairly steady rate. Other applications,
usually on small systems, may have to carry a high surge of air if several machines happen to be operated at the same time.
Then there may be a period with almost no flow.
To make a realistic estimate of air flow volume, the far right column of the chart showing compressor HP may be used. On
steady pumping, a compressor will produce a minimum of 4 SCFM air flow for each 1 HP of capacity. This is a conservative
figure, as most compressors will produce 5 or 6 SCFM.
For example, a 25 HP compressor will produce at least 100 SCFM of air as shown in the far left column on the same line as
25 HP.
excerpted from
Industrial Fluid Power
, Volume 1, third edition, 1984
SCFM
Air Flow 25
50
75
100
150
200
300
500
1000 Compressor
HP
4
½
½
½
½
½
½
½
¾
¾
1
12
½
½
½
¾
¾
½
¾
1
1
3
20
¾
¾
¾
¾
1
¾
1
1¼ 1¼
5
30
¾
¾
1
1
1
1
1¼ 1¼ 1¼
7½
40
¾
1
1
1
1¼ 1
1¼ 1½ 1½
10
60
1
1
1¼ 1¼ 1¼ 1¼ 1½ 1½ 2
15
80
1
1¼ 1¼ 1¼ 1½ 1¼ 1½ 2
2
20
100
1¼ 1¼ 1½ 1½ 1½ 1½ 2
2
2½
25
120
1¼ 1½ 1½ 1½ 2
1½ 2
2½ 2½
30
160
1¼ 1½ 1½ 2
2
1½ 2½ 2½ 3
40
200
1½ 2
2
2
2
2
2½ 3
3
50
240
1½ 2
2
2
2½ 2
2½ 3
3
60
300
2
2
2
2½ 2½ 2
3
3
3½
75
400
2
2½ 2½ 2½ 3
2½ 3
3½ 4
100
500
2
2½ 2½ 3
3
2½ 3½ 3½ 4
125
Air