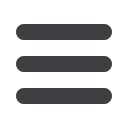
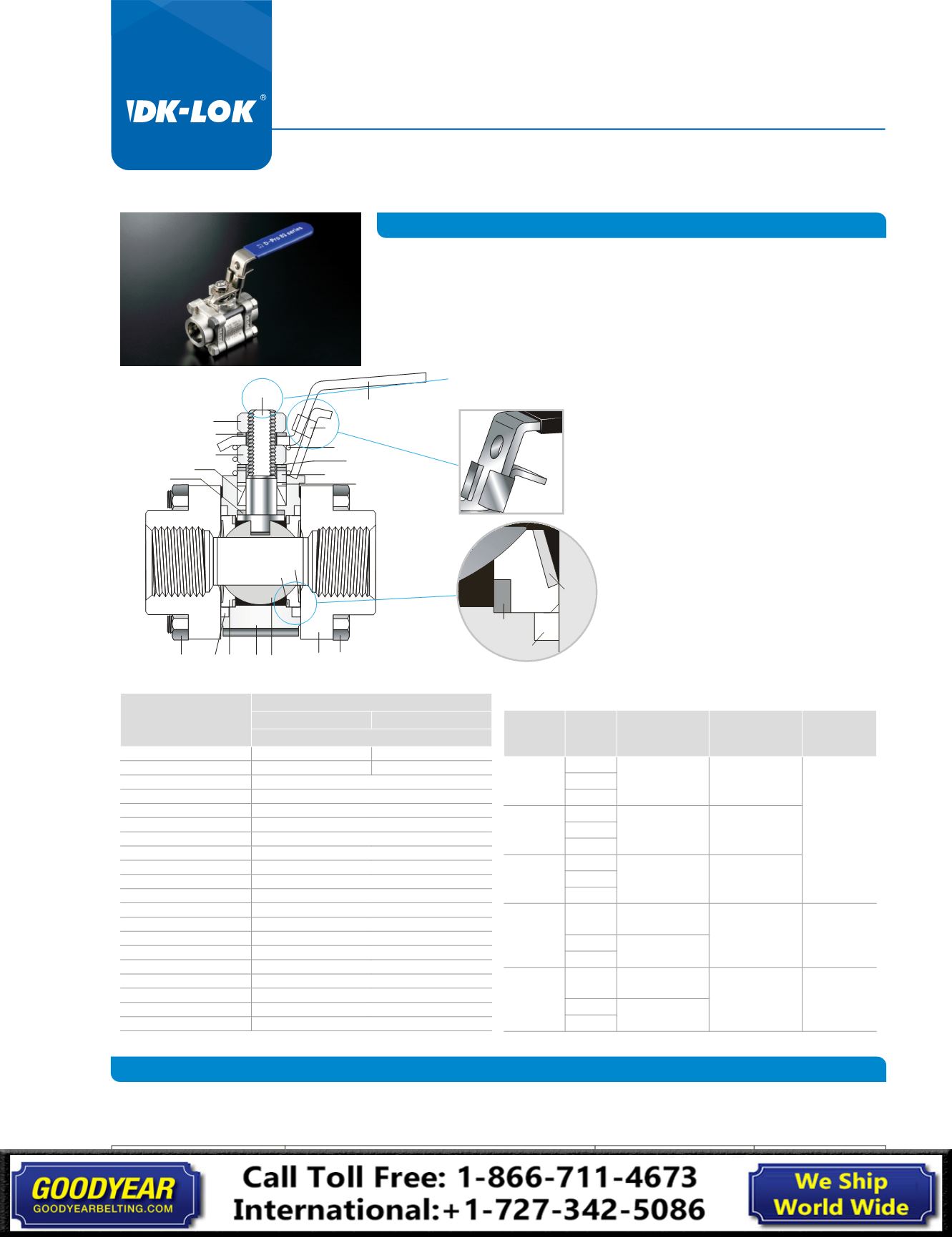
Valves
DK-LokTubeFittingCerti cationListing
DK-LokValveCerti cationListing
QualitySystemApprovals
13
9
8
2
1
5
3
4
10
6
7
14
11
11
19
20
12
15
16
17
18
Seat
Ball
Seat
Support Ring
Disc
Spring
Flange Seals
No.V83-5
July 2013
V83 Series Swing-Out Ball Valves
Pressure Rating up to 3,000 psig (206 bar)
Features
Factory Test
Table 1.
Material of Construction
Component
Valve Body Materials
Stainless steel
Carbon Steel
Grade / ASTM Specification
1. Body
CF3M / A351
WCB / A216
2. Flanges (2)
CF3M / A351
WCB / A216
3. Ball
Type 316 / A276
4. Seats (2)
See Table 2.
5. Flange Seals (2)
PTFE
6. Disc Spring (2)
Strain Hardened SS316
7. Seat support rings (2)
Type 316 / A276
8. Body fasteners (4)
SS316 Gr.B8M/ A193
9. Body hex nuts (4)
SS316 Gr.8M/ A194
10. Stem
Type 316 / A276, A479
11. Stem Nuts (2)
SS316
12. ToothWasher
Stainless steel
13. Handle
SS304 with Vinyl sleeve
14. Locking Device
SS304
15. Grounding spring
SS312 / A313
16. Stem Springs (2)
Strain Hardened SS316 / A240
17. Gland
Type 316 / A276
18. Packing Support
PEEK (Polyetheretherketone)
19. Upper & Lower Packing
Reinforced PTFE
20. Stem Bearing
PEEK, Optional X750
·
Wetted parts and lubricants are listed in
blue
.
Table 2.
Seat Materials
Pressure - Temperature Ratings
Seats
Valve
Series
Pressure Rating
@ -28 to 38 °C
(-20 to 100 °F)
Pressure @Max.
Temperature Lubricants
Standard
Reinforced
PTFE
V83A
151 bar
(2200 psig)
7 bar @ 232°C
100 psig @450°F
Silicon based
and
PTFE based
V83B
V83C
Virgin
PTFE
V83A
103 bar
(1500 psig)
7 bar @ 232°C
100 psig @450°F
V83B
V83C
Carbon
PTFE
V83A
172 bar
(2500 psig)
7 bar @ 232°C
100 psig @450°F
V83B
V83C
PEEK
V83A
206 bar
(3000 psig)
55 bar @ 232°C
800 psig @ 450°F PTFE based
V83B
172 bar
(2500 psig)
V83C
UHMWPE
V83A
206 bar
(3000 psig)
17 bar @ 121°C
250 psig @ 250°F
Hydrocarbon
based and
PTFE based
V83B
172 bar
(2500 psig)
V83C
Every valve is tested with nitrogen @ 68.9 bar (1,000 psig) for leakage at the seat to a maximum allowable leak rate of 0.1 SCCM.
Shell test with nitrogen @ 68.9 bar (1,000 psig) is performed to a requirement of no detectable leakage with a liquid leak detector.
Shell test with water at 1.5 times the working pressure is performed on request with extra cost.
• Pressure and temperature compensation seat design.
• Swing-out design for fast and easy maintenance with the valve in-line.
• Chevron packing design.
• 2-way (on-off) valves with quarter-turn actuation.
Two flats on stem (10) and lever handle (13) indicate open or closed
position of the valve.
Built-in manual locking device (14) allows locking the
valve with a detent either in open or closed position.
Youmay also apply a pad-lock to this device. Pad-lock
hole: 8 mm (0.314 in.)
Compensation seat design requires no
pressure to create a seal.
Under high pressure, seats react on the ball
movement for sealing at upstream and
downstream.