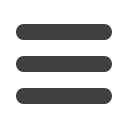
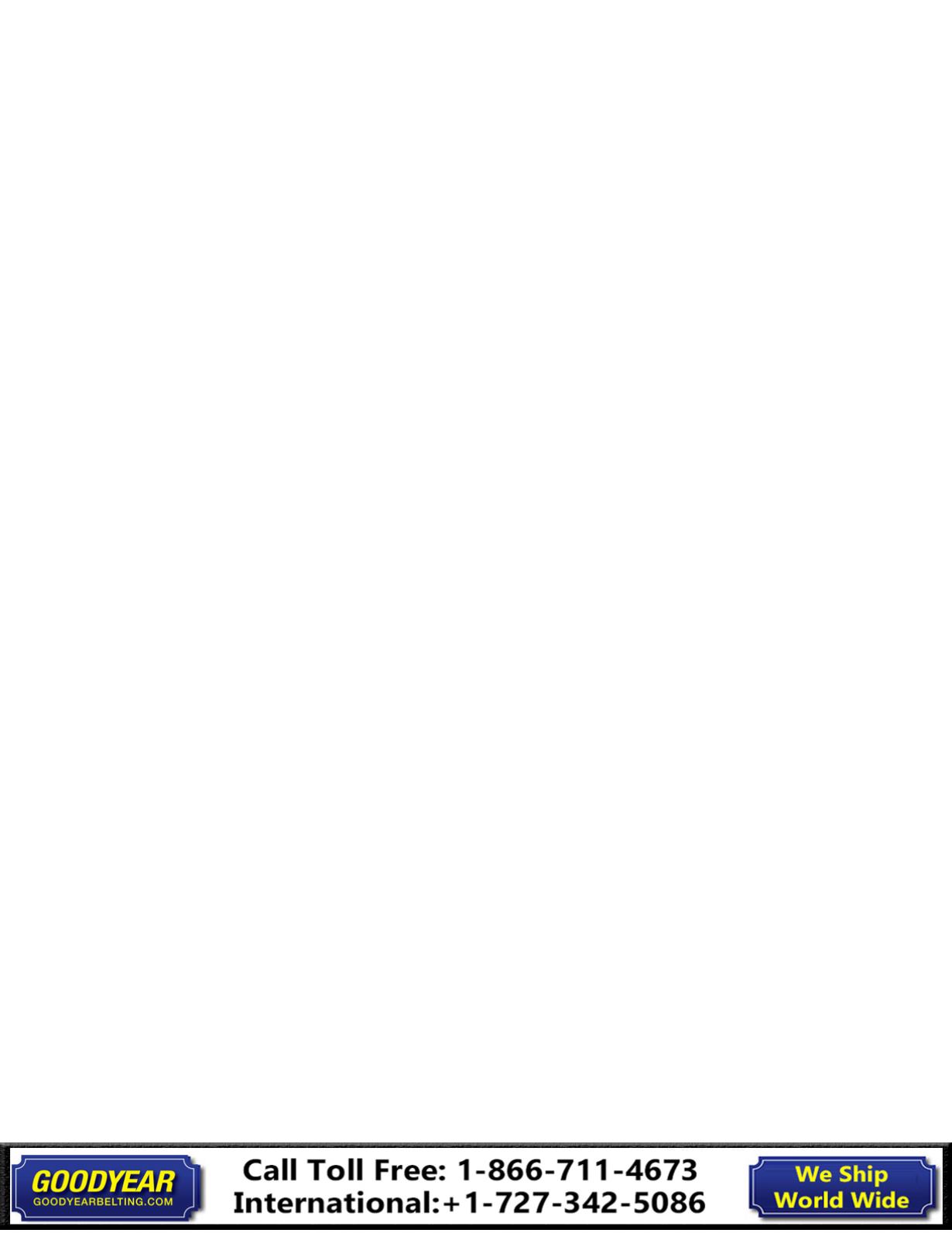
42
Flexsteel
®
Belts
A Technically Superior Product
Generations of our engineers have been involved for
over 70 years in the design and application of Flexsteel®
conveyor belting. This cumulative experience translates into
state-of-the-art technology, assuring superior product design
and maximum performance for our customers.
Superior strength, durability, ease
of installation
ContiTech's Flexsteel® conveyor belting has provided maximum
protection against pounding and abuse in some of the world's
largest and most demanding applications. Flexsteel® belting is
the only choice when extremely high tensions are present,
having proven itself on copper and oil sands system operations
at 6000 PIW (ST7000) tension.
Flexsteel® is also the preferred belt on long overlands and short
Stacker systems where minimum belt elongation is a critical
design consideration. Flexsteel®’s steel cord reinforcement
elongates a maximum of .25% at rated tension, allowing for
acceptable take-up travel design on long overlands, as well as
short Stacker/Reclaimer systems.
We have the capability to manufacture Flexsteel® belts in long
lengths up to 168 in. (4.2m) roll diameters, or 50 short ton
(45.4 M.T.) rolls at some production locations. This allows for
the minimum number of splices or joints in a conveyor system,
which facilitates faster installation while providing a more
reliable system. Specialized oblong packaging is available to
further maximize belt lengths.
Additional time can be saved during installation by using
another Flexsteel® innovation: Preform™ Splice kits. Preform™ is
a pre-grooved form that simplifies splicing by allowing you to
“sandwhich” the cables coming from either side between the
formed rubber. Not only is the process of splicing made easier,
but the belt itself is made stronger.
You can depend on Flexsteel® steel cord belts to be precisely
engineered to meet rigorous manufacturing standards. Rely on
Flexsteel® for strength, durability and ease of installation.
There are three component parts to
Flexsteel® belting, each one critical to
belt performance:
Zinc galvanized steel cord
Flexsteel® belts are designed by selecting cord construction
to provide the best specification for a particular application.
The cords, made up of many wire filaments, are constructed
to provide high flexibility, low elongation and permit efficient
and high strength splice designs. The galvanized zinc coating
produces a bonding agent between the cord and insulation
gum and provides an important barrier against corrosion.
Insulation gum (core rubber)
Extensive rubber compounding technology has enabled
Flexsteel® engineers to develop a superior insulation gum
bonding rubber, which penetrates and adheres to the steel
cords. The result is excellent adhesions, corrosion resistance
and splice efficiencies.
Outer rubber covers
The advanced compounds in Flexsteel®’s top and bottom
covers are designed to protect the steel cord strength member
against the abusive environmental conditions prevalent in most
conveying applications. Compounds are available to withstand
abrasion, jagged cutting and gouging, high impact, sub-zero
temperatures, moderate heat, hardening effects of ozone
attack and fire propagation. Special service compounds are
available for unique applications, such as the oil sands in
Canada, which require a compound that withstands both low
temperatures and oil.
2015 Heavyweight Conveyor Belts
Flexsteel®