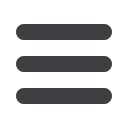
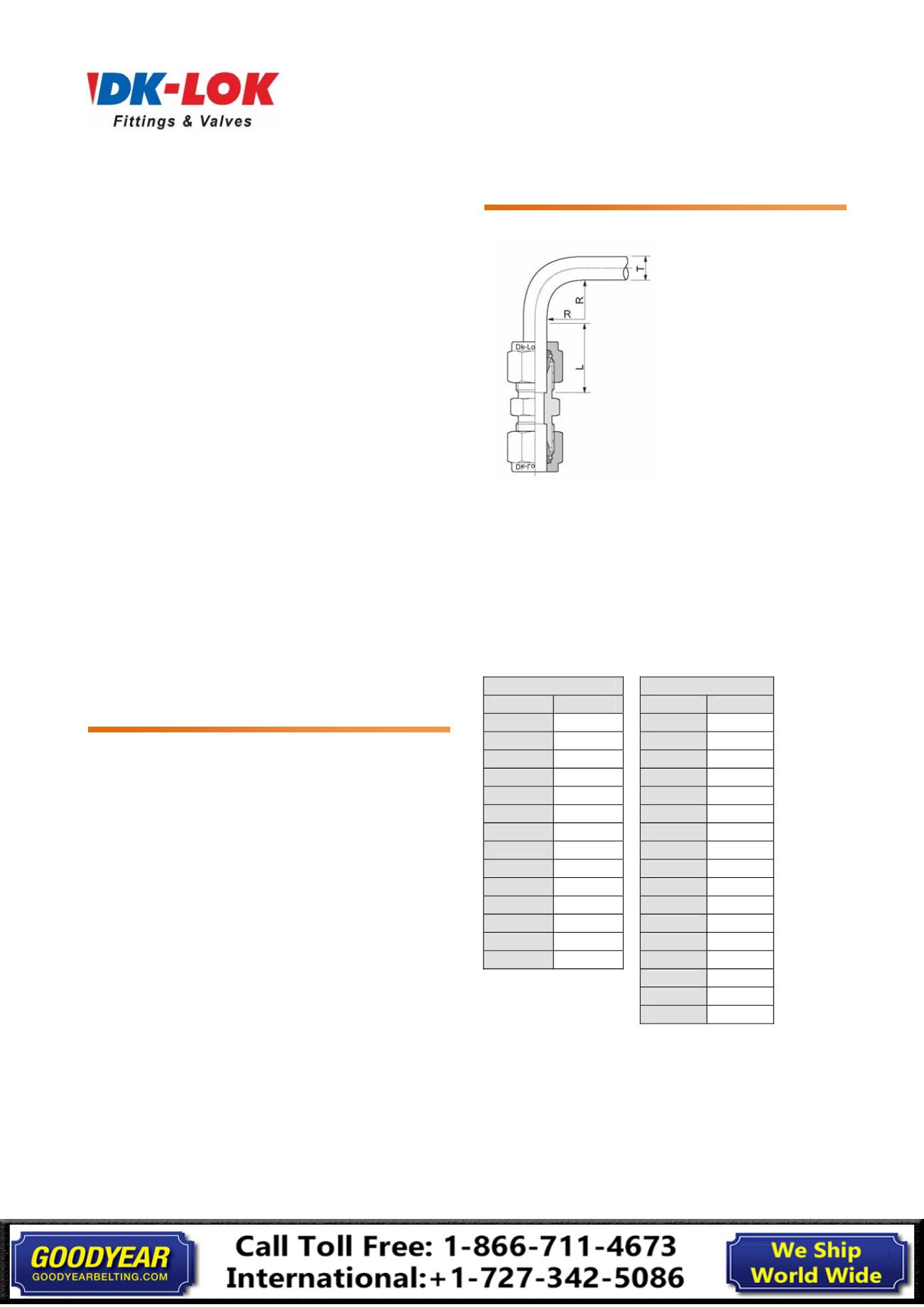
Stainless Steel Instrumentation
Fractional / Metric Tubing
TS-04-S
2011
2 of 6
www.dklok.com5. Material
Using like tubing and fitting material is essential for
the thermal compatibility and corrosion resistance.
Different materials have different hardness level that
may adversely affect the fitting seal on tubing. The
only exception is copper tubing with brass DK-LOK
fittings.
6. Wall thickness
The table 4 and 5 show tubing working pressure
ratings in a wide range of wall thickness. A too thin
of a wall may collapse and too thick wall may not
properly be deformed by the ferrule action.
DK-LOK fittings are
not
recommended for tube wall
thickness not listed in the table 4 and 5.
7. Wall thickness for gas application
Gases such as nitrogen, air, hydrogen and helium,
can escape even the most minute leak path due to
their small molecules
.
Heavy wall tubing resists
ferrule action by coining out minor defects of the tube
surface whereas a thin wall may collapse with little
resistance to ferrule action. For gas service, use
heavy wall
in white
in table 4 and 5.
8. Weld tubing
The weld bead should not be noticeable visually on
the outside of the tube.
Note:
Tubing of ornamental, structural or mechanical grade should not
be used for fluid system.
2). Tubing Handling
Careful handling and storage practices will protect tubing
from unnecessary scratches, nicks and or degrading good
tubing surface finish.
Tubing ends should be capped so any foreign
materials will not fall inside during transportation and
storage.
Do not drag across tubing rack, cement, gravel or
any rough surface.
Do use correct tube cutter for tube material. The
wrong cutter may result in excessive deformation of
the tube end.
Do not cut deep with each turn of cutter.
Tube cutters and hacksaws should be sharp enough.
Hacksaw blades should have at least 32 teeth per
inch.
Deburring tube ends before inserting in the tube
fittings helps prevent against system containments.
3). Tubing Installation
T: Tube OD
R: Radius
L: Straight tube length
When tube bend is too close to a fitting, the bend section
shall enter the fitting. This may not allow the tube to be
bottomed out in the fitting, and may result in leakage.
Keep the proper straight length of tube as shown in table 1
below.
Do not bend a tube in the fitting. Use tube bender.
Table 1.
Fractional tube
, in.
Metric tube,
mm
T
L
T
L
1/16
1/2
3
19
1/8
23/32
6
21
3/16
3/4
8
23
1/4
13/16
10
25
5/16
7/8
12
31
3/8
15/16
14
32
1/2
1-3/16
15
32
5/8
1-1/4
16
32
3/4
1-1/4
18
32
7/8
1-5/16
20
34
1
1-1/2
22
34
1-1/4
2
25
40
1-1/2
2-13/32
28
46
2
3-1/4
30
50
32
54
38
63
50
80